Ytalia : Thiết bị & Công nghệ sản xuất lốp Ô TÔ
The new generation of INTEREUROPEAN's Fully Automated Tire Assembly Machine offers a fully automated solution for making high-performance tires with single-stage technology, has received worldwide recognition and nominations for the “International Tire Technology Award for Innovation and Excellence 2015” by International Journal of Tire Technology.
Uni-Stage TBM is equipped with an active guidance system for all rubber components, an automatic cutting and application system, flat drum tire assembly technology, an advanced monitoring and control system with communication touch screen computer interface and advanced receipt management and diagnostics.
The granulation feeding into the granulator is carried out by the robot, while the unloading of the green tire's finished product from the single-stage drum is carried out by the transfer ring.
c woven fabric, IL+SW online/offline pre-assembled, Tread out of Spool/Precut to length, Separate on Application Sides or Walls
The single-stage drums used in the machine can be supplied by INTEREUROPEAN (dual/single/mechanical type) or the machine can be designed to use the Customer's own standard single-stage drum
The configuration machine can be tailored to any customer specifications, including 1 or 2 layers, single and double-drums used to achieve cycle times of 30 seconds/ times in top machine configuration
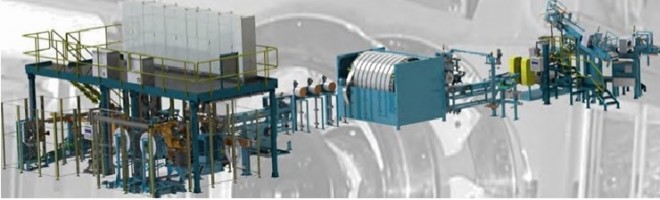
INTEREUROPEAN can provide a pre-assembled line for in-line pre-assembly + Offline sidewalls with machinery to reduce costs and increase productivity of Uni-Stage TBMs.
Total machine cycle time depends on drum type and maintainer configuration and varies from 30 to 35 seconds per tire in fully automatic mode.
As an option, Innerliner and Sidewalls can be applied separately on single-stage drums to maximize tire design flexibility and optimal joint distribution across the tire's circumference. Separate Sidewalls Server with ultrasonic cutting and electronic guidance system provides fully automated application for single-stage drum upper sidewalls.
The machine cycle time increase in this case is only 5 seconds
The special tapes with beads and separators come from the company's famous Floating Bead Line, which operates in a fully automatic mode and is equipped with a robot that places the beads and separators on the tape. One beading line can produce enough beads for two Uni-Stage TBMs and is supplied as standard with the builder.
The new generation of breaker maintainers allows for high speed applications and breaker head-to-head connections on the bottom drum by magnetic conveyors. Active guidance of the breakers is carried out by high resolution cameras, while the length measurement is checked by various electronic systems, allowing the material length to be evenly distributed across circumference of the drum.
Spiral nylon coating is applied immediately after the cutter by a high speed application head with tension control system which ensures constant material tension during different application stages.
At the next station, the spike strip is applied out of the spool. The barbed strip is automatically applied and cut on the drum after application with the ultrasonic blade. This application system, known as 7/8, gives the utmost accuracy in tire matching, as positioning tolerances are limited to the short end of the remaining material which will be applied after cutting through the drum. . The ultrasonic cutter has a longitudinally adjustable cutting angle, which allows for extremely low angle cuts, thus greatly increasing the contact surface between the spike layers in the splice area and making the joint almost zero. visible to the human eye. A multi-disc propeller roll with adjustable pressure stitches the tire during material application on the drum. The active guide system ensures the correct centering of the spikes before application.
After tire application, a transfer ring lifts the belt & tire pack from the cutter drum and transfers it to the single-stage drum on the pre-shaped carcass. Final shaping, dynamic stitching, and unloading of the green tire with the transfer ring complete the machine's cycle
Each departure station is equipped with a pair of detachable carriages. This allows the service technician to replace the bobbin outside the discharge station while the machine continues to operate. Replacing a train car with a new one is simply transferring the carriage and joining the ends of the material in the loose station. This system allows for very quick spool changes, reducing machine downtime.
The Uni-Stage TBM control system is designed with a modular architecture using the latest hardware components available on the market. Based on customer preference, the machine can be supplied with Allen Bradley or Siemens PLC and components.
A touchscreen HMI is supplied as standard, with a dedicated display and graphical interface for all machine functions, recipe management, extensive alarm handling and production statistics.
Other optional components and servicers can be added, such as
Chafers, strips, nylon caps, etc... Different versions of single stage drums (revolving/mechanical type), break drums with motorized diameter adjustment and full turning rings can be supplied according to required to accelerate tire size changes.
Interesturopean Uni-Stage TBM mills are supplied with motorized adjustments of all important machine parameters according to recipe settings. This includes motorized conveyor angle adjustment based on new drum diameter, centering device adjustment based on material width, stitch device adjustment based on new tire size, and more.
All these additional functions help to reduce the time required for resizing, which is key to achieving the winning combination of high flexibility and high production output in the tire making system. this new,
Standard configuration of Uni-Stage . Tire Making Machine
One. Indexing Body with two drums one-story construction
NS. Splice control system to check the application of components on the drum
NS. Index Tower with Two Breaker Drums, Covering Full Diameters
NS. Mobile ring device with set of segments, covering a full range of diameters
e. Laser position marking system with automatic positioning (3 pcs.)
NS. Multi-disc type stitching rolls for stitching components during application
NS. Automatic beading ring,
Robot for automatic placement of the beads into the bead setters Automatic Server for carcass components
One. Configured to produce a two-layer tire construction
NS. Four component discharge stations, one of which is dual station (for side wall)
NS. Active guide system for inner and side panels
NS. Mechanical pre-centering on release stations for inside and layer
e. Automatic cut-to-length system for all semi-finished components
NS. Automated super-assembly system for inner lining and sidewalls
NS. Conveyors feed components from discharge stations to application conveyors
NS. Automated mobile application conveyor with proactive centering of components before application on drum.
I. Multi-disc type stitching rolls for stitching components during application
NS. Sensor to detect spool change joints and material folds on component feeders
k. Material presence sensor inside the spool
l. Powerful host mainframe to eliminate vibrations during operation.
Automatic Server for Belt & Tread assembly components
One. Servers for First and Second Cutter with bottom contact type application system, including cutting and application conveyors.
NS. Dual discharge stations for each breaker to minimize downtime when changing spools
NS. Automatic length guide and cutting system for cutters
NS. Additional breaker length control system after cutting to double check the actual breaker length and its correct distribution on the drum circumference by motor synchronization
e. Automated host for Spiral Nylon Coating (JLB) with single application head. Optional dual application heads are available on request for special type applications.
NS. Large capacity with tension control system
NS. Tension control and adjustment device, integrated into the JLB application head.
NS. Automatic Tread Server with dual discharge station for quick spool changes
I. New and upgraded version of the multi-step active guidance system for tires during application just prior to application on drums
NS. Ultrasonic type cutting device for tire cutting after application on drum, up angle adjustable C:\IE Site photo to 15°
k. Multi-disc tire stitching rolls with adjustable pressure
l. Sensor to detect spool change joints and material deformation on the feed conveyor
NS. Material presence sensor inside the spool
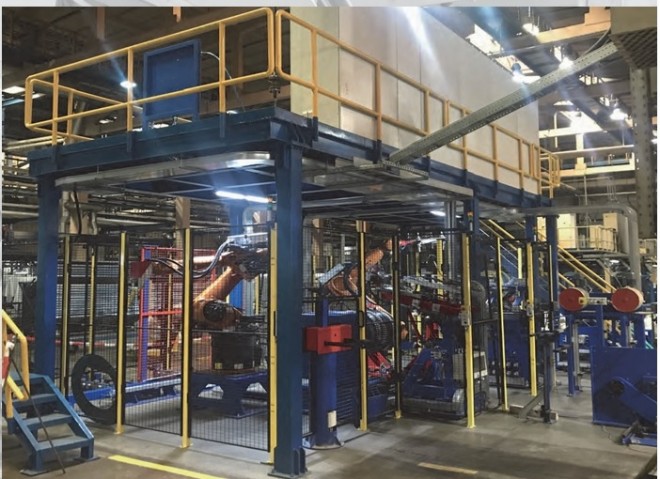
Dynamic Green Tire Stitching Device
One. Fully automatic sewing device with automatic setting of all seam parameters when resizing, according to new receipt settings
NS. Ability to sew tires of different configurations (TOS or SOT)
Tires Automotive Integrated Tire Assembly (ITAC) to produce 2.5 million tires/year
The Integrated Tire Assembly Cell (ITAC) consists of the following components:
• 4 fully automatic tire assembly machines
• 2 Apexing Beads Necklaces
• 1 bead wrap
ITAC is designed to produce 8000 automatics per day or 2.5 brands per year and it is capable of producing 4 size options at the same time.
ITAC requires 6 operators to operate the complete system (1 for each tire assembler, 1 for the two bead lines and 1 for the bead wrapping line). Operators also provide spool replacement and feed their machines.
After the beads arrive at the Bead Apexing Line, they are automatically loaded into the machine by a robot. After the top is applied, the granules are unloaded by the same robot and placed into the mobile truck, which is separated by special plastic washers. The mobile truck is then automatically routed to one of the four Tire Assembly Machines (TAMs), which generate the corresponding tire size.
Cumulative rounds for incoming trucks on each TAM have enough capacity to ensure uninterrupted tire production for 24 hours.
Each Bead Apexing Line performs one size change every 12 hours of operation (or 4000 beads), providing two TAMs with two different sizes of peaked beads.
The conveyor and truck handling is controlled by an integrated control system, which manages the entire production process and controls all the machines working within the ITAC system.
The control of bead production, crest application and tire assembly is done in automatic mode by means of a camera and plate laser system, checking the accuracy of material application and joint quality at every step of the assembly process.
The automatic resizing operations allow to minimize production loss due to frequent resizing, while the availability of 4 Independent Tire Assembly Machines inside the system allows optimization of the performance of the tire. them by dedicating each machine to a specific tire size and only making rapid changes of tire size within the same bead diameter. Such an approach allows for a significant increase in production flexibility, and it is possible to produce many small tires without significant production loss.
INTEREUROPEAN tools and drums, available in both Uni-Stage and 1st & 2nd Stage versions, can be tailored to the customer's manufacturing process and specifications. As an option, the machine can be customized to use the customer's own existing drum, provided that does not affect the operation of the machine.
The new generation of the Fully Automated Granulation Line, offered as part of a fully industrialized ITAC system, is operating at various tire factories.
ITAC systems can be supplied in Uni-stage or Combi configurations, depending on customer preference and manufacturing processes.
Tire size range covers all PCR & LT tires up to 24", including extreme performance tyres.
Beads are produced directly within the ITAC system on dedicated bead winding lines, which can be supplied in configurations for square or hexagonal bead production.
The produced granules are automatically unloaded from the drum and loaded onto the trays, which are then automatically transferred to one of the two Apexing Bead Wires for further Apex application..
Uni-Stage TBMfor PCR & LT Tires
Technical Data | PCR-LT20 | PCR-LT24 |
Bead Diameter (inch) | 13”-20” | 15”-24” |
Green tire diameter | 800mm | 1000mm |
Bead Setting width – max | 600mm | 700mm |
Breaker drum diameter | 750mm | 980mm |
IL+SW complex width, max | 1000mm | 1200mm |
1st Ply width | 900mm | 1000mm |
2nd Ply width | 900mm | 1000mm |
Sidewalls width max | 240mm | 260mm |
Steel/Textile chafers width | 25mm – 90mm | 25mm – 90mm |
Breaker width | 280mm | 350mm |
Breaker cutting angle | 18° - 30° | 18° - 30° |
Tread Band width | 350mm | 450mm |
Tread length | 2500mm | 3200mm |
JLB/Spiral Nylon Overlay width | 10mm - 25mm | 10mm - 25mm |
| | |
PLC type | Allen Bradley SLC 5000 | Allen Bradley SLC 5000 |
Pneumatics | FESTO | FESTO |
Cycle time per carcass | 30 sec. | 40 sec. |
Production output, up to | ~2500 tires/day * | ~2000 tires/day * |
Operators required | 1 machine operator | 1 machine operator |
Required floor space (with 2 plies configuration) | 12.510 x 12.940mm | 13.010 x 13.450mm |
(*) - depending on production conditions, skill level and efficiency
COMBI TBM is a new tire building system for PCR & LT tires, combining first- and second-stage TBMs into one fully automatic machine capable of producing a finished green tire every 35 seconds without any manual operation at all. The production output of such a system is up to 2,000 tires per day.
Ưu điểm chính của hệ thống đóng lốp mới này là nó cho phép khách hàng giữ nguyên quy trình đóng lốp hai giai đoạn hiện có và vẫn được hưởng lợi từ tất cả các lợi thế của việc lắp ráp lốp hoàn toàn tự động. Nó cũng mang lại sự linh hoạt trong thiết kế lốp xe mà chỉ một quy trình hai giai đoạn mới có thể cung cấp, và sản lượng sản xuất cực cao với mức giá hợp lý.
Diện tích của hệ thống là khoảng 11 x 12m và nó chỉ cần một người vận hành giám sát trực quan quá trình lắp ráp lốp. Ứng dụng sản phẩm trên trống và chất lượng mối nối được kiểm soát bởi máy ảnh CCD kết hợp với laser ánh sáng.
Belt & Tread ServersHệ thống làm lốp mới này được phát triển bằng cách kết hợp tất cả kiến thức và nhiều năm kinh nghiệm sản xuất mà INTEREUROPEAN tích lũy được vào một chiếc máy mới.
Khoảng 80% thiết kế của nó bắt nguồn từ các giải pháp kỹ thuật công nghiệp hóa hoàn toàn tự động hiện có, hoạt động trên nhiều TBM INTEREUROPAN mới nhất, trong khi 20% còn lại được thiết kế riêng cho hệ thống này.
Các nghiên cứu về thời gian chính xác, Kỹ thuật 3D và mô phỏng chuyển động đã được công ty thực hiện để đảm bảo rằng tất cả các bộ phận của máy hoạt động hết công suất và không bị mất thời gian trong chu kỳ máy.
Hệ thống sản xuất lốp COMBI mới bao gồm 5 trạm chính, hoạt động cùng lúc. Thời gian chu kỳ của mỗi trạm bằng hoặc thấp hơn 35 giây, đảm bảo tốc độ đầu ra không đổi của một lốp xanh thành phẩm cứ sau 35 giây.
Các hạt được đưa vào bộ định hạt của trạm thu dọn bằng một robot được thiết kế đặc biệt. Các băng cassette đặc biệt với các hạt và bộ tách đến từ Dây chuyền hạt nổi nổi tiếng của INTEREUROPEAN, cũng hoạt động ở chế độ hoàn toàn tự động và được trang bị một rô bốt để đặt các hạt và bộ tách vào băng. Dây chuyền Apexing một hạt có thể sản xuất đủ hạt cho 2 COMBI TBM và thường sẽ được cung cấp cùng với các máy xây dựng dưới dạng một gói.l.
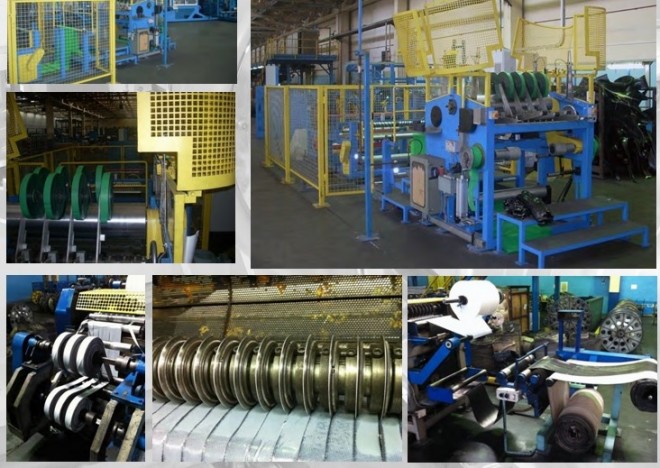
Các thành phần thân thịt như Innerliner, Ply 1 và Ply 2 được tự động căn giữa bằng hệ thống dẫn hướng chủ động, được cắt trước theo chiều dài và được áp dụng trên trống loại REC Giai đoạn 1 tại Nhà ga Tòa nhà N.1. Cắt bên trong được thực hiện bằng thiết bị cắt siêu âm đặc biệt với góc cắt có thể điều chỉnh theo chiều dọc. Giải pháp này cho phép cắt góc cực thấp, do đó tăng bề mặt tiếp xúc giữa các lớp lót trong trong khu vực mối nối để tránh bất kỳ khả năng bám khí nào. Cuộn chân vịt đa đĩa đặc biệt giúp đẩy không khí ra ngoài trong quá trình ứng dụng vật liệu trên trống, trong khi các con lăn bên được thiết kế tùy chỉnh cung cấp cho việc khâu các mép của vật liệu, treo trên trống.
Tại cùng một trạm, các hạt được rô bốt đặt vào bộ định hạt ở đầu mỗi chu kỳ và thực hiện các thao tác cài đặt và xếp hạt. Lớp thứ hai có thể được áp dụng trước hoặc sau khi vận hành lần lượt để tạo ra sự linh hoạt tối đa cho thiết kế lốp.
Ở trạm tiếp theo, các thành bên được tự động áp dụng và cắt trên trống sau khi ứng dụng bằng hai lưỡi siêu âm độc lập. Hệ thống ứng dụng này, được gọi là 7/8, cho phép độ chính xác tối đa của việc ghép các thành bên, vì dung sai định vị chỉ giới hạn ở phần đuôi ngắn của vật liệu còn lại để áp dụng sau khi cắt qua tang. Các thiết bị cắt siêu âm được trang bị góc cắt có thể điều chỉnh theo chiều dọc, cho phép cắt góc cực thấp, do đó tăng đáng kể bề mặt tiếp xúc giữa các lớp thành bên trong khu vực mối nối để làm cho mối nối gần như không thể nhìn thấy bằng mắt người. Các cuộn chân vịt đa đĩa đặc biệt khâu các thành bên trong quá trình ứng dụng vật liệu trên trống. Các cạnh của thành bên, treo trên trống, được hỗ trợ bởi các con lăn tương phản đặc biệt, cho phép.
Technical Data | COMBI-1320 | COMBI-1524 |
Bead Diameter (inch) | 13”-20” | 15”-24” |
Green tire diameter | 800mm | 1000mm |
Bead Setting width – max | 600mm | 700mm |
Breaker drum diameter | 750mm | 980mm |
IL (or IL+Chafer) width, max | 1000mm | 1000mm |
1st Ply width | 1000mm | 1000mm |
2nd Ply width | 1000mm | 1000mm |
Sidewalls width max | 240mm | 260mm |
Steel/Textile chafers width | 25mm – 90mm | 25mm – 90mm |
Breaker width | 280mm | 350mm |
Breaker cutting angle | 18° - 34° | 18° - 34° |
Tread Band width | 350mm | 450mm |
Tread length | 2500mm | 3200mm |
JLB/Spiral Nylon Overlay width | 10mm - 25mm | 10mm - 25mm |
| | |
PLC type | Allen Bradley SLC 5000 | Allen Bradley SLC 5000 |
Pneumatics | FESTO | FESTO |
Cycle time per carcass | 35 sec. | 40 sec. |
Production output, up to | ~2000 tires/day * | ~1500 tires/day * |
Operators required | 1 machine operator | 1 machine operator |
Required floor space (with 2 plies configuration) | 11 x 12 m | 12 x 13 m |
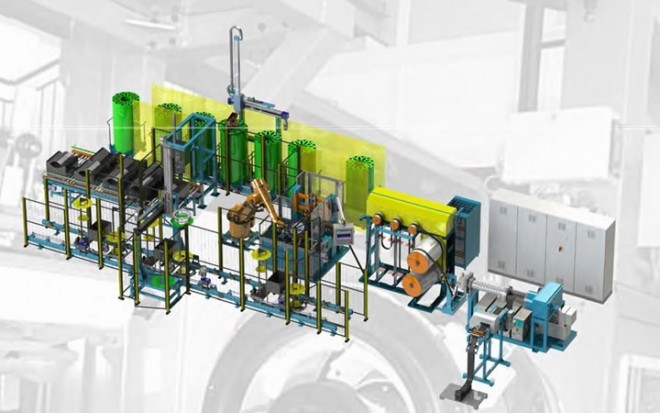
Automatic 1st Stage TBMfor PCR & LT ties
Các TBM Giai đoạn 1 & Giai đoạn 2 của Interesturopean cung cấp giải pháp hoàn toàn tự động để chế tạo lốp hiệu suất cao với công nghệ 2 giai đoạn.
TBM Giai đoạn 1 được trang bị hệ thống hướng dẫn tích cực cho tất cả các thành phần cao su, hệ thống cắt và ứng dụng tự động, công nghệ lật ngón tay xuống và bàng quang, hệ thống kiểm soát và giám sát tiên tiến với giao diện máy tính màn hình cảm ứng và chẩn đoán và quản lý biên nhận tiên tiến.
Thời gian chu kỳ máy thấp nhất là 45 giây cho mỗi lốp ở chế độ hoàn toàn tự động. Người vận hành chỉ kiểm tra hoạt động của máy bằng mắt thường, dỡ thịt thành phẩm ra khỏi thùng vào cuối mỗi chu kỳ và nạp hạt mới vào máy.
Cấu hình máy có thể được điều chỉnh cho phù hợp với bất kỳ thông số kỹ thuật nào của khách hàng, bao gồm 1 hoặc 2 lớp, thép hoặc vải dệt, thành bên từ cuộn hoặc băng độc lập, dải lắp ráp trước, v.v..
Technical Data | Values |
Bead Diameter (optional) | 13”-17” (15”-20”) |
Drum width (optional) | 250mm-550mm (250mm-600mm) |
Innerliner width (optional) | 720mm (800mm) |
1st Ply width (optional) | 720mm (900mm) |
2nd Ply width (optional) | 720mm (900mm) |
Sidewalls width max (optional) | 240mm (300mm) |
Textile chafers width (optional) | (30mm – 50mm) |
| |
Cycle time per carcass | Approx. 45 sec. |
Operators required | 1 machine operator |
Required floor space (with 2 plies configuration) | 5.780mm x 9.685mm |
| |
PLC type | Allen Bradley SLC 5000 |
Pneumatics | FESTO |
Main power supply voltage | 380 V / 50 Hz / 3 phase |
Control Voltage | 220V / 48V / 24V |
Pressure (dry air) | 6 bar |
Vacuum | By supplied vacuum pump |
| |
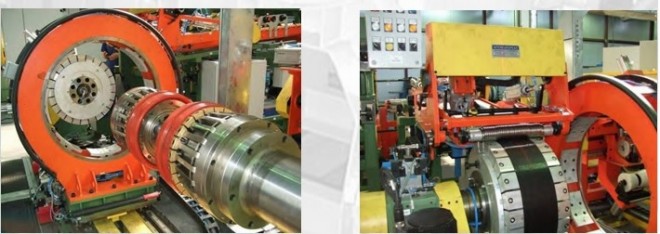
Automatic 2nd Stage TBMfor PCR & LT TiresCác TBM Giai đoạn 1 & Giai đoạn 2 của Interesturopean cung cấp giải pháp hoàn toàn tự động để chế tạo lốp hiệu suất cao với công nghệ 2 giai đoạn.TBM Giai đoạn 2 được trang bị hệ thống dẫn hướng tích cực cho tất cả các thành phần cao su, hệ thống cắt và ứng dụng tự động, trống ngắt đôi trên tháp pháo quay để tối ưu hóa thời gian chu kỳ, trống định hình kiểu khóa hạt, rãnh ra khỏi ống với cắt siêu âm, lớp phủ nylon xoắn ốc (JLB) hoặc nylon capply, hệ thống kiểm soát và giám sát tiên tiến với giao diện máy tính màn hình cảm ứng và quản lý và chẩn đoán biên nhận tiên tiến.Thời gian chu kỳ máy thấp nhất là 45 giây cho mỗi lốp ở chế độ hoàn toàn tự động. Người vận hành chỉ kiểm tra hoạt động của máy bằng mắt thường và dỡ các lốp xanh thành phẩm ra khỏi vòng chuyển, trong khi chu trình máy vẫn tiếp tục.Cấu hình máy và các tùy chọn có thể được điều chỉnh cho phù hợp với bất kỳ thông số kỹ thuật nào của khách hàng.
Dây chuyền bơm hạt thế hệ mới nhất 13 ”- 22” này được INTEREUROPEAN thiết kế và chế tạo dựa trên kinh nghiệm sản xuất nhiều năm tại các nhà máy sản xuất lốp xe khác nhau và với các hợp chất cao su khác nhau, có một số ưu điểm quan trọng so với các máy bán tự động thế hệ trước , nhu la:
- • Tự động thay đổi kích thước
- • Không còn tế bào quang để định vị trống, chỉ cần một động cơ không chổi than với bộ mã hóa
- • Hệ thống nối chắc chắn được đồng bộ hóa hoàn toàn
- • Máy đùn loại chân 80mm mạnh mẽ hơn nhiều với sản lượng tăng lên để sản xuất kích thước hạt lớn hơn
- • Vận hành máy đùn tốc độ không đổi để có được cấu hình đỉnh không đổi
- • Dây treo được kiểm soát độ căng công suất cao
- • Các ngón tay nối cấu hình có thể điều chỉnh để có chất lượng mối nối tối đa và tính đồng nhất
- • Hệ thống điều khiển dựa trên PLC Allen Bradley thế hệ mới nhất với quyền truy cập từ xa tùy chọn để khắc phục sự cố và tích hợp hệ thống điều khiển nhà máy cấp 2
- • Hệ thống kiểm soát chất lượng mối nối và chiều cao Apex trực tuyến với xử lý dữ liệu thống kê
- • Các TCU Máy làm lạnh và Máy đùn tuần hoàn nước mạch kín thế hệ mới
- • Hoạt động hoàn toàn tự động với rô bốt KUKA tùy chọn để nạp / dỡ hạt và thao tác để chèn các vòng phân tách
- • Độ tin cậy cao và chất lượng ứng dụng không đổi
FILLER APPLICATION UNITThe Filler Application Unit in equipped with vertical filler guiding channel, dual hot blades for cutting of the trailing end of the filler and three drums on a rotating shaft dividing the filler application into 3 steps:
- application,
- splicing
- unloading of the beads with filler and loading of the empty bead
Bead centering on the drum is guaranteed by the radial expansion of the drum segments.
Application is performed by dual stitching disks with adjustable angle, strongly pressing the filler base to the bead
from both sides. The pressure applied during application can be easily adjusted according to process requirements, while
stitching from both sides provides maximum grip between the filler and the bead, and allows for using the bead of non-boxed shape (hex, round etc.)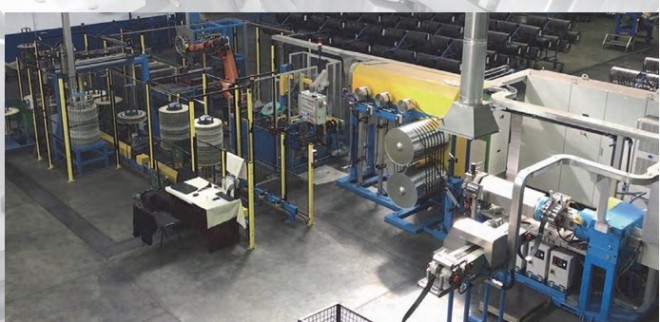
Beads feeding to the system is realized using cassette type feeding station with beads placed into 8 boxes with 50 sections each, keeping the beads separated all the way up to the pick-up position by the robot. Beads feeding into the cassettes is easy and quick and can be done directly at the bead winding line.
Availability of 8 cassettes allows the operator to fill 7 of them with beads while one is working in the station, giving approx. one hour of gap between the feeding operations. Same concept is used for the trucks feeding and unloading from the system. Provided accumulation capacity allows for approx.. one hour]time between the operator calls for trucks loading/unloading operations.
Separate 2-axis manipulator is installed in the system for separator rings placement between the beads on the trucks.
FLIPPER APPLICATION STATION (optional)
The automatic Flipper Application Station is an optional component of the Bead Apexing Line, which can be added to the standard line without influencing the production output of the main system.
This latest generation Bead Filler Line 17,5”- 24,5” was designed and built by INTEREUROPEAN based on the many years of production experience in different tire factories and with different rubber compounds,
The main strong points of this line are:
- Fully automated operation with KUKA/FANUC robots for beads and separator rings handling
- Duplex 90+90 mm Cold Feed Extruder with increased output for producing wider profiles
- Constant speed extruder operation for getting constant apex profile
- Special design Air Cooling System with automatically adjustable pre-set temperature
- High capacity free loop with optional automatic cutting to length station for slabs
- Beads feeding directly from an integrated bead winding line, or from bead trucks with automatic carousel type feeder
- Fully synchronized robust automatic apex splicing system
- Adjustable splicing fingers for maximum splice quality and uniformity
- Automatic rubber side strip application from bobbin or by using a Triplex Extruder
- Automatic Fabric Flipper application and turn-up
- Optional online Apex height and splice quality control systems with statistics data processing
- Latest generation Allen Bradley/Siemens PLC based control system with optional remote access for troubleshooting and level 2 factory control system integration
- Automated size change based on the recipe settings
High reliability and constant quality of application
has a long experience in design and development of automatic and semi-automatic Bias Cutter and Splicer Lines for steel and textile cord plies.
There are various types of bias cutters with many configuration options:
- Fully automatic cutting and splicing
- Automatic cutting and manual splicing
- Chafer/strips let-off and preassembling in-line
- Various cutting angle and material width ranges
Every machine configuration is designed according to the customer’s specifications.
Fully automatic Bias Cutters and Splicers for PCR tires are available in overlapped splice and butt joint configurations. Line speeds of up to 20 splices per minute can be achieved in fully automatic mode.
Selling 50% shares of aluminum granule factory.
(Additives for the steel industry).


Currently, our company is building a factory to produce aluminum particles (the most important additive for the steel industry).
Capacity: 1000 tons of aluminum granules/month
Location: No. 02 Nam Song Cam Street - Hong Bang District - Hai Phong (On an area of 2000 m2).
Total investment includes: Land + Factory + Production line of 1000 tons of aluminum granules/month + Office & other infrastructure items.
The total value of the factory is 24 billion VND
Now our company needs to sell 50% of the factory shares, each 1% share is 240 million VND.
Dear investors, please cooperate with us. Please come to our company office at: No. 02 South Song Cam Street - Hong Bang District - Hai Phong, to view the property and discuss cooperation issues. Or contact Mr Son: 0903446210
Note: Profit of 01 ton of aluminum granules when ex-factory is about 5 million VND/ton.
FORMOSA steel every month they have to buy 5000 tons of aluminum granules
Hồ sơ đấtĐăng ký kinh doanh 
TECHNOLOGY CHART OF ALUMINUM BENE PRODUCTION LINE

Equipment list for aluminum granule production line 2 tons/hour:
1 – furnace electromagnetic induction aluminum melting TQ-600 Kw–02 Furnace.
2 – American aluminum wire extrusion machine 137 Kw – 02 Machines.
3 – Japanese AMADA wire cutting machine 110 tons – 02 machines.
4 – Power transformer station 560 KVA – 01 station
5 – Power transformer station 1000 KVA – 01 station
6 - Sản xuất 01 tấn nhôm hạt - Cần 750 Kw/giờ
Standard metal composition in alloys:
Al ≥ 96%
Si ≤ 0,50%
Cu ≤ 0,25%
Zn ≤ 0,10%
Aluminum grain size (Ø, 13 mm - long, 15mm)
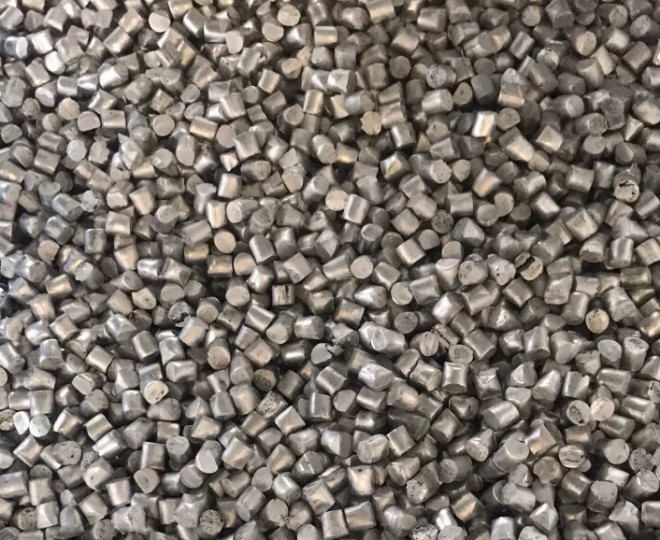
Selling price of aluminum granules on the international market.Aluminum Alloy Ingot (LME) Price + Grain Processing Cost = Aluminum Grain Price
For example, the price of aluminum granules in October 2021
(LME Alloy Aluminum) $2,634 + (Machining) $500 = $3,134 U SD

Plant for the production of vegetable oilsPreparation is the first step in the oilseed removal process. The best method of preparation will depend on the type of oilseed and the expected market for the products created after removal. oil.
MÁY CẮT PHÔI THÉP NÓNG

Specially designed for : Continuous casting machines in steel mills. It is used for hot workpiece cutting.
Horizontal during construction and moves with hot workpiece at wheel speed for precise cutting.
It helps to reduce overall operating costs such as Oxygen Gas, LPG Gas,
Reduce loss of materials & Labor. This machine is suitable for 3/6, 4/7 & 6/11 Radius Continuous Casting Machine, to cut workpiece sizes from 100 x 100 mm to 160 x 160 mm at 900°C. Our machine will work. smooth motion and widely demanded for optimum performance, durable support and high dimensional accuracy.
Will never compromise on quality and is capable of manufacturing world class quality and delivering state of the art products. Our vision is geared towards the needs of our customers' satisfaction.
Higher productivity.
Reduce production costs at every process stage.
Optimizing production facilities and resources
Apply environmentally friendly and resource-saving technologies.
Produce items and provide services of outstanding quality and/or unique characteristics.
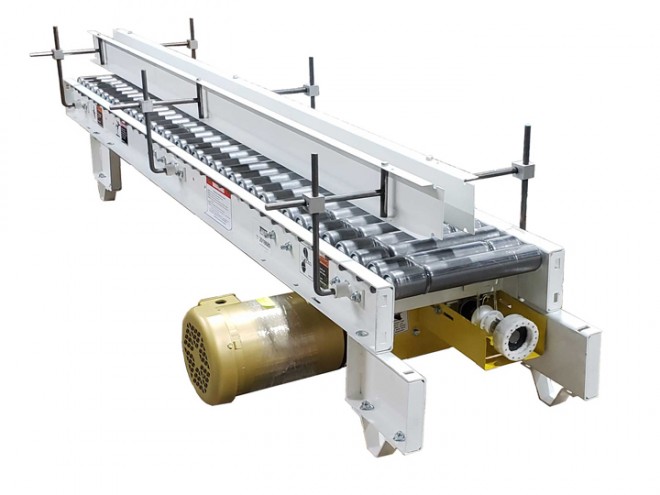