Sheet steel production line Germany Supplying equipment & technology transfer
STEEL: GREAT POTENTIAL AS AN INNOVATIVE MATERIAL
Nothing short of revolution, our Molded Casting Technology (BCT®) is a further leap towards near-net-shape casting. Depending on the type of BCT® wheel you choose, you can run different production levels and produce a variety of products. What makes BCT ® so special is that they handle alloys that are not suitable for continuous casting. In addition, the new technology also responds to conventional crack-critical steels that can not be produced by continuous casting.
THE CONCEPT
MANUFACTURING BY LOCAL AND INTERNAL GOODS
German plate production line
Equipment supply & technology transfer
German plate production line-Equipment supply & technology transfer

MANUFACTURING BY LOCAL AND INTERNAL GOODS
New to steel production is our BCT® - Casting Belt Technology for casting horizontal netting shapes near flat steel products. BCT is a leap in casting technology designed to produce special steels as well as conventional steels.
Just imagine the benefits of the BCT Small Grinder - a process called inlining. It means that the BCT process takes place in a stream with hot rolling process.
MORE INFORMATION
ENERGY SAVING PROCEDURE
Our micro plants use full cast iron technology, specially designed to cut energy consumption and CO2 emissions.
Frozen fast
Low deformation energy Not hot
THÊM THÔNG TIN

TECHNOLOGY
New steel products need new molding process
Forget bending or straightening
Protected against oxidation, liquid steel is poured from the normal into a covered container.
Then, it passes through a submerged fountain submerged into the pre-heat feeding system. Next, the steel flowing into the horizontal mold moves including the conveyor belt and the internal cooling dam. There is an inert gas atmosphere above the conveyor belt to protect the hard steel. Finally, at the rear of the wheel, a specific gas mixture directly affects the solidification structure.
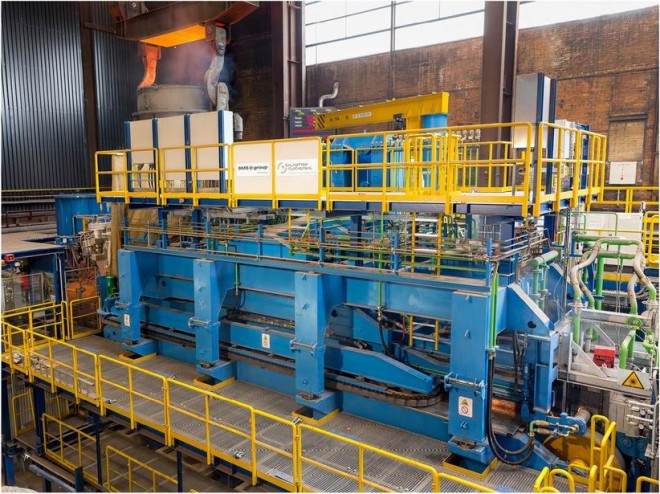
FEATURES OF IMPRESSION
Flat tension in the horizontal direction:
Not bent or straight
Cast without powder:
Steel has high aluminum content as possible
Mold Travel, not oscillations:
Flat ribbon surface that does not oscillate mark
fast casting, high casting speed, low casting thickness:
Fine particle cast structure has no risk of isolation
Inert atmosphere and independent indirect cooling:
There is no scale formation during the casting process
Deformation at 8-20 mm gauges:
High quality hot strip

BCT ® :
Process and main characteristics
Casting smooth
Casting line from conveyor belt horizontally. Then, it enters an enclosed roller table to ensure complete process planning to the bottom of the table. The next in the row after the roll sheet is a combination of two pinch-rolls separated by a looper. This part not only transports the precast strip, it also isolates the product from the downstream effects. Unit rolls second pinch feed strip for a hydraulic breaker move. In order to ensure the required plate length, the cutting line travels at the same speed as the molding strip. Now a roller table accelerates up to 9-m-long sheets toward the end of the rollers table, where they slow down again. Finally, the pusher placed the plates on a hydraulic lift table.
LỢI ÍCH
Wheels on your request
New steel products require new molding processes
Lightweight and safe design based on high energy absorption
Custom product attributes
Technical solutions and new design for components
Extremely versatile, the wheels combine with both BOF and arc furnace stores. What's more, we design your BCT® installation according to your specific needs. You can produce wide strips as well as wide strips of heat. Whether you have small, medium or high production capacity, we design your factory to fit you.
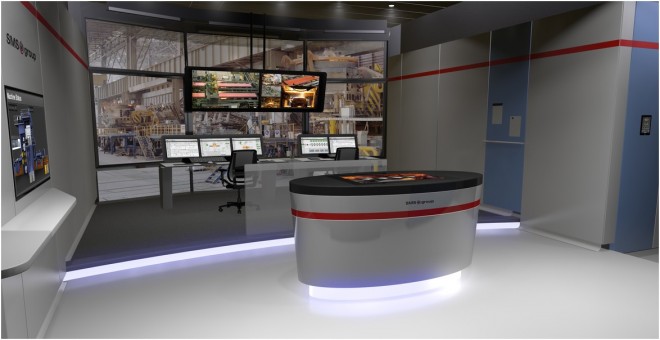