Vấn đề & Giải pháp
Advanced incineration technology Incineration is a heat treatment technology used to reduce the volume of waste to be disposed of in the end. Incineration can often reduce the volume of waste by more than 90% and it is one of the widely used technologies to treat municipal solid waste before disposal in landfills. Most modern incineration plants incorporate heat recovery as well as power generation facilities to recover the heat energy in the waste. 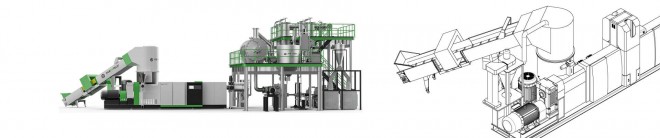 | To ensure that emissions meet stringent standards set by regulatory bodies (e.g. European Union Industrial Emissions Directive 2010/75/EU) for public health and In order to protect the environment, modern incineration plants adopt a number of advanced designs and control processes and emissions with cleaning measures as illustrated by the flowchart below: | Biểu đồ quy trình đốt điển hình
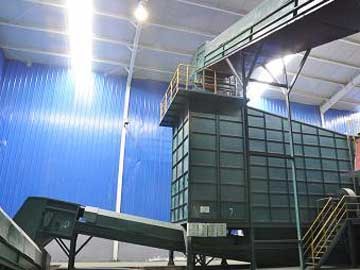 | Incineration - Waste is continuously fed into the furnace by an overhead crane. Waste is burned in a specially designed furnace at high temperature > 850 o C for more than 2 seconds with sufficient air supply to ensure complete combustion of the waste and prevent the formation of dioxins and carbon monoxide.
Steam boiler/turbine - Heat from combustion is used to generate steam in the boiler. The steam then drives the turbine which is coupled to the generator. The excess heat generated can also be used for other purposes, for example swimming pool heat. Exhaust gas cleaning - Boiler exhaust is typically cleaned using the following advanced pollution control systems to ensure compliance with stringent environmental standards: | 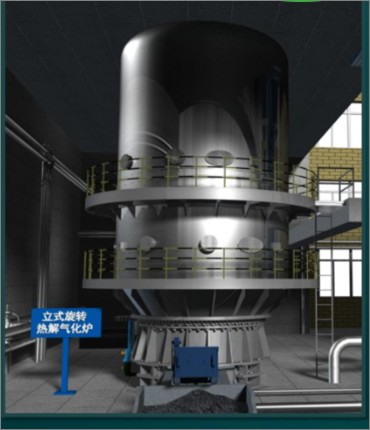 | l Dry or wet scrubbers - spray lime powder or fine atomized slurry into the hot exhaust gas to neutralize and remove acidic pollutant gases (sulfur oxide, hydrogen chloride) l Activated carbon injection - to absorb and remove any heavy metals and organic pollutants (e.g. dioxins) in the exhaust l Bag house filter - to filter and remove dust and fine particles l Selective Non-catalyst Reduction - to remove nitrogen oxides (the cause of urban smog) by reacting them with ammonia or urea. Ash residue treatment - Ash residue from combustion generally includes bottom ash and fly ash from flue gas cleaning equipment. Bottom ash is either reused as construction material or disposed of in landfills. Fly ash is usually stabilized and solidified with reagents (e.g. cement) and disposed of in a dedicated landfill with continuous environmental monitoring. Ash smelting technology that uses heat energy in an incinerator to melt ash residue at high temperatures is a technology used in some places. The smelted products are inert and do not contain hazardous materials so that they can be reused (e.g. building materials). The ash smelting is relatively more expensive but it has the advantage of further reducing the volume and immobilizing any hazardous materials in the fly ash. | |
|
STAVN helps you survive in the waste recycling business.
STAVN specializes in municipal solid waste sorting and recycling solutions and equipment. With a team of over 20 years of global know-how and experience, STAVN is confident in providing practical and reliable waste recycling solutions. STAVN provides a full service on the technological side, from conceptual design to planning, manufacturing, assembly supervision, component start-up and maintenance to complete recycling and sorting systems.
Service Stavn
Stavn provides not only high quality plants, but also a full range of services to our customers. According to different requirements of different customers, we can make specific business plan for them. This team consists of experienced engineers and technicians, responsible for helping customers with preliminary assembly and commissioning of plants.
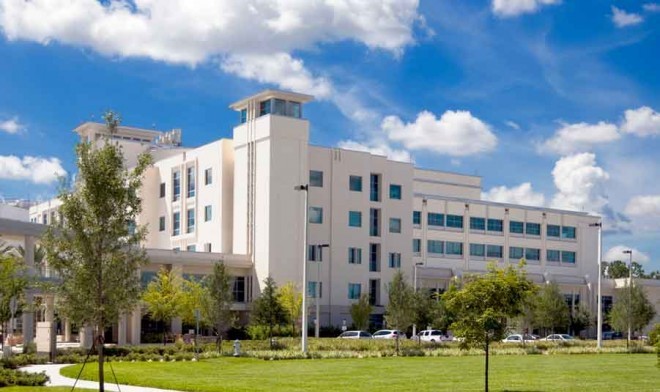
Washing powder factory - China
Equipment supply and technology transfer
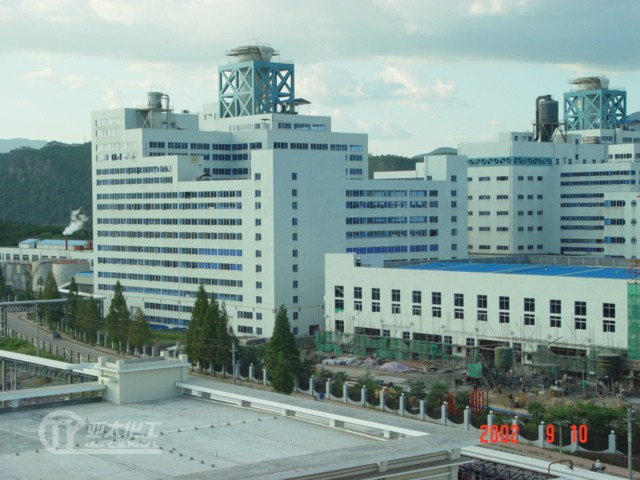
Three types of plants can be supplied according to the required density of the product.
1. Washing powder factory with spray drying tower: The final detergent product from this type of plant will have a high density from 0.25 to 0.35.
2. Detergent powder factory with accumulation technique: mainly for producing high density detergent with a density from 0.45 to 0.80.
3. High-Concentrate Tower Blends: Combining the technical advantages of high towering and agglomeration, it is possible to produce both high density and low density by a factory.
Full automatic or manual computer control systems can be used in the above factories, depending on the requirements of the customer.
The capacity of the plants is 3000t / y to 200000t / y.
The operation mode can be manually and control the computer.
The scope of supply is from the renovation of the existing factory to the construction of a completely new factory. Environmental Impact: No waste water discharge.
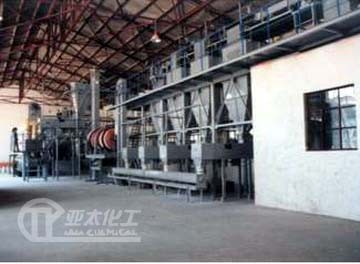
Three types of plants can be supplied according to the required density of the product.
1. Dry powdered plant with spray drying tower: The final detergent powder from this type of plant will have a high density of 0.25 to 0.35.
2. Detergent powder factory with accumulation technique: mainly for producing high density detergent with a density from 0.45 to 0.80.
3. The detergent plant has both towering and agglutinating techniques: combining the technical advantages of high towering and agglomeration, the ability to produce both low density and high density bleach High by a factory.
Full automatic or manual computer control systems can be used in the above factories, depending on the requirements of the customer.
The capacity of the plants is 3000t / y to 200000t / y.
The operation mode can be manually and control the computer.
The scope of supply is from the renovation of the existing factory to the construction of a completely new factory. Environmental Impact: No waste water discharge.
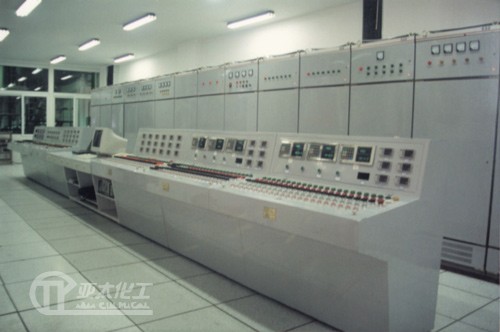
Ingredients in the form of powder and liquid are accurately quantified, then brought to neutral and the aging system is neutralized and aged. The muddy stream process now passes through a homogeneous milling machine to be homogeneous. Subsequently, the sludge was introduced into the spray drying tower to produce hollow particles with a density of 0.20 to 0.35 kg / L, particle size from 0.5 to 1.5 mm. After sieving and conditioning in an air system, the powder becomes a low density dough base. An additional after-meal unit can be supplied upon request of the customer, where the perfume, enzyme, perborate is mixed with the original powder to form medium or high-grade detergent.
Solid materials in powder form are sieved and pre-mixed, then stored in the respective silos. Solid materials are weighed accurately by conveyor belt dosage form of detergent powder, and mixed feed. While liquid materials are accurately quantified by quantitative dosing and feed aggregates in spray form. The aggregate product from its bottom is put into a liquid layer to remove free water in the surface of the grain and form crystal water in the powder to increase its added value. Fragrances, enzymes and other small components are added to this powder after added to reach the final high-end product with a high density of 0.45 to 0.8 kg / L, waiting for packaging.
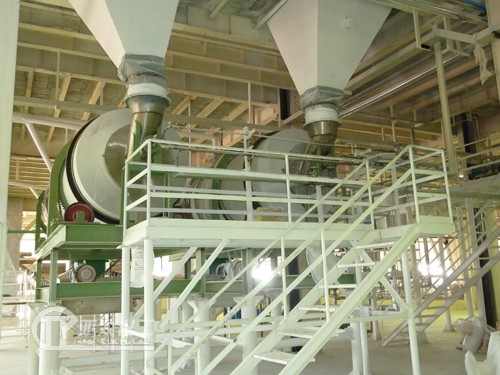
1. The whole factory is controlled automatically by PLC
2. The startup and shutdown of the factory are controlled by the programs in the computer.
3. There are interlocks between the device's critical equipment, and operational monitoring data.
4. The functions of the system include adjusting the detergent powder; print report, display activity data and record / filing.
5. The big screen shows how the factory is running. There are also alarms and instructional interventions.
6. Manual and automatic modes can be switched between different operators.
7. All materials, both solid and liquid, are automatically quantified according to computerized detergent formula.
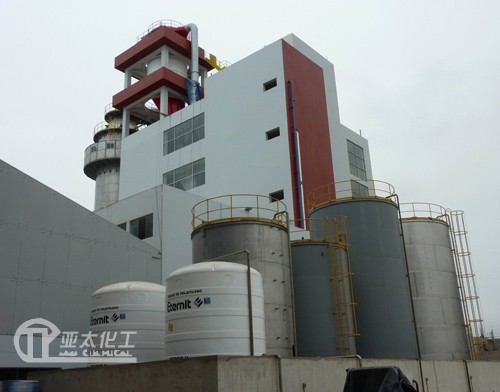
This plant can produce both high density and low density detergents with a high density of 0.28 to 0.7 kg / l. Energy is saved a lot because 70% of the material is added by the accumulation system.
Three types of plants can be supplied according to the required density of the product.
1. Dry powdered plant with spray drying tower: The final detergent powder from this type of plant will have a high density of 0.25 to 0.35.
2. Dry powdered factory with accumulation technique: mainly for producing high density dough powder with high density from 0.45 to 0.80.
3. The detergent plant has both towering and high agglomeration technologies: combining the advantages of high towering and agglomeration techniques, it is possible to produce both low density elevation by a factory.
Full automatic or manual computer control systems can be used in the above factories, depending on the requirements of the customer.
The capacity of the plants is 3000t / y to 200000t / y.
The operation mode can be manually and control the computer.
The scope of supply is from the renovation of the existing factory to the construction of a completely new factory. Environmental Impact: No waste water discharge.
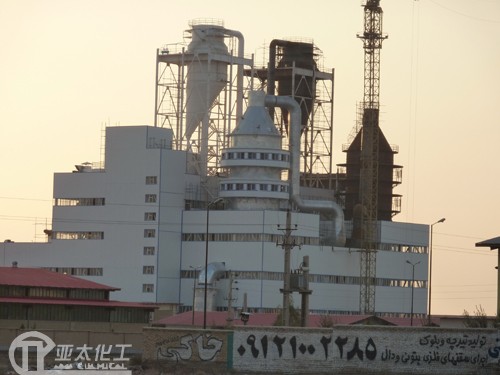
Three types of lines can be supplied as follows:
1. Washing powder with spray tower: The final washing powder of the product from this sugar will have a high density from 0.25 to 0.35.
2. Washing wire with synthetic technology: mainly for producing detergent powder with high density from 0.45 to 0.80.
3. Washing powder with towering and high agglomeration technology: Combining the technical advantages of high towering and agglomeration, it is possible to produce both low density and high density detergents. follow a road.
Full automatic or manual computer control systems can be used in the above factories, depending on the requirements of the customer.
The capacity of the plants is 3000t / y to 200000t / y.
The operation mode can be manually and control the computer.
The scope of supply is from upgrading existing lines to completely new ones. Environmental Impact: No waste water discharge.
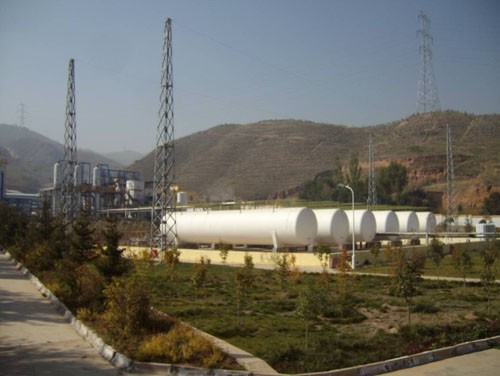