-Building factory infrastructure, (Including land for 10 hectares): 20 million USD.
1-Primary aluminum is an extremely important input material for many different commodity production industries, for all countries in the world.
2- The price of primary aluminum on the international metal floor in the last 10 years has often shifted from : 2500 USD - to 3000 USD/ton.
3-Analysis table: Production cost for 01 ton of aluminum finished product, factory.
Price of primary aluminum at LME London 11/2021 is:
According to the writer of this project: When Vietnam Aluminum Corporation is born and put into operation, it will have a stable and stable profit of: 300 USD / 1 ton -
Revenue: 480,000 tons x 3,000 USD/ton = 1.296 billion USD/year.
Profit: 480,000 tons x 300 USD/ton = 144 million USD/year.
Thoughts of the project writer: I must confess to you, after 30 years of working with the profession: Importing equipment and transferring production technology for many different industries. After a while of researching about the primary aluminum production project in Vietnam, until today, sitting down to write these words, I really have not escaped: Surprise and shock. A new, new project. Look at it, it sounds very gentle, simple, but behind it is a very ghostly profit-seeking system. A project with a total investment of 600 million USD and a profit of 144 million USD per year, actually I can't explain why.?
1-If making primary aluminum is very profitable, why not increase the output to a few million tons/year but only at 480,000 tons/year.?.I would like to tell you the Alumina output of 02 Nhan Co and Tan factories. Rai is 1.4 million tons, only enough to produce 700,000 tons of primary aluminum per year.
2-Currently, EVN Group is buying electricity from thermal power plants: 0.08 USD, equivalent to 1,840 VND/Kw/hour and they are also buying electricity at private hydropower plants at 1,100 VND/Kw/hour.
3-Why not accumulate a 56 ton/hour factory but divide it into 04 14-ton/hour factories.? I would like to tell you: The author of the project intends to: Split the project - Stick to the MINI Hydropower plants, to buy cheap electricity.
So if aluminum plants can buy electricity from private hydropower plants, its profit is very high.
4-Comparison between two industries: Steel production and aluminum production in Vietnam.
Then for every investment of 550 million USD-Each year, 01 million tons of billet steel can be produced, the selling price is 700 USD/ton, so the annual revenue is 700 million USD, 1 year profit is 70 million USD.
DA.Điện gió 88 MGW 150 triệu USD 44 MGW 33 triệu USD 33 triệu USD
If you place aluminum plants near private hydropower plants and satisfy them with the purchase price of 1,400 VND/Kw/hour, the profit will skyrocket to 60 million USD/year.
I think projects like this. The State has a policy of guaranteeing credit, including interest payments of 12%/year, which is normal.
Open letter: Invitation to invest.
Dear domestic and foreign investors. As we have shown above. This is a very special project, the investment rate is very low but the investment efficiency is very high, this is a very unique investment project in Vietnam today. We are the researchers who set up the project, but do not have the financial capacity to implement and implement it. So, investors, please think carefully about this project.
Please travel with us . You are the leaders of Vietnam Aluminum Corporation in the pre-insurrection period. We believe that, one day, when there is no commune here, Vietnam will be at the top of the list of countries exporting commercial aluminum.
Best regards.
TEL ; 0903.446.210
(Các tỉnh có thể đặt nhà máy nhôm :
Đắk Nông + Lâm Đồng + Bình Phước + Bình Thuận + Ninh Thuận + Đắc Lắc).
*The most important issues for investors:
Please note that Vietnam's Anumina powder production and electricity output are still very modest, only enough for aluminum manufacturers: Producing 500,000 tons of primary aluminum in a year. If you don't care about it right away. When the sharks on foreign aluminum production have kept an eye on. That also means there is no field for you to play.Sản lượng nhôm nguyên sinh của các quốc gia trên thế giới :
(tại đường linhk phía dưới)
https://en.wikipedia.org/wiki/List_of_countries_by_primary_aluminium_production
Technological process of producing primary aluminum:
Mining bauxite;
Extraction of alumina (aluminum oxide) from bauxite;
Electrolysis of aluminum from alumina;
Processing of molten aluminum and casting into ingots.
Technical Documentation - 1Technical Documentation - 2Technical Documentation - 3Danh sách các nhà sản xuất nhôm trên thế giới
https://en.wikipedia.org/wiki/List_of_aluminium_smelters
Main aluminum electrolysis
Metallic (primary) aluminum is smelted from alumina by electrolysis by the Hall-Heroult method. It takes place in electrolytic cells, which are a reservoir of molten cryolite. This molten criolite electrolyte is in this electrochemical process. A typical electrolytic cell is about 5-10 m in length. The cathode in electrolysis is the bottom of the electrolytic bath, lined with carbon blocks.
The anodes are large clumps of carbon, gradually immersed in cryolite as they burn. Therefore, carbon anodes require constant replacement, and it is an important part of the work and cost. Cryolite (Na 3 AlF 6 ) is practically not consumed during electrolysis.
Alumina is gradually added to the electrolytic cell from the top of the molten, where it is melted. The temperature in the electrolysis bath is 950-970°C. Drops of liquid aluminum form and accumulate at the bottom of the bath. This is the main aluminum. The molten aluminum leaves the cell at a temperature of about 900°C.
The direct current, supplied to the cell, is usually 4-5 volts and amperage of about 150000 A.
Producing 1 kg of aluminum requires about 2 kg of alumina, 0.5 kg of coal and 15 kWh of electrical energy.
An electrolysis plant can consist of 600-700 electrolyzers and is up to 1 km in length.
Treating virgin aluminum
On the territory of an electrolytic plant is usually a casting unit, where the minimum fluid flow paths come from the primary aluminum housing electrolyzers. The foundry has large, electrically heated reverb furnaces (mixers).
Typically, to improve product quality, two reverb furnaces are connected in series. A furnace - a "storage tank" - is designed to receive, maintain, and average the temperature and chemical composition of metals. Another furnace - "filling" or "dispensing" - is designed to mold a wide variety of products. Typically, these furnaces are stationary, unlike inclined furnaces that allow for a continuous casting process.
Liquid aluminum is kept in the furnace for 30-45 minutes at a temperature of 690-730 °C for the floating and precipitation of non-metallic impurities, and the evolution of gas from the metal.
Impurities are removed from molten aluminum by refining. To do this, it is usually washed with chlorine. Aluminum chloride in the gaseous form is formed, passes through the melting process, envelops the impurity elements, rises to the metal surface in the form of slag, is mechanically removed. Chlorinated aluminum also removes Na, That, Mg and dissolved gases in aluminum. After refining, the purity of primary aluminum reaches 99.5-99.85%.
Cast aluminum in the mold
Ingot castings - in the form of small ingots - are usually produced in a mold on a conveyor belt of a filling machine. the metal cast in the mold is a short flat ray. After filling the mold with the surface of the metal oxide film is removed. These machines are equipped with a mechanical stamping mechanism and an air or water cooling system of the mold.
Primary aluminum economic geography
The main materials in the production of primary aluminum are:
1-bauxite;
2-hard coal (coke) and
3-Electric energy.
Unfortunately, these three components are never in the same place in the world. Therefore, it is often chosen for the location of primary aluminum production near hydroelectric power plants with cheap electric energy. These plants can be several thousand kilometers away from aluminum and aluminum ingot supplies.
Detailed presentation: Technological process
The mixture of cryolite solution with dissolved alumina concentrate electrolytically causes liquid aluminum to move towards the cathode and accumulate on this anode while the C anode cathode is oxidized to carbon dioxide. The power used by many of these furnaces is usually very low voltage (usually 3-5 V), but requires large currents – in each electrolysis chamber the amperage can be from 220kA[1] ] up to 340kA.[2] Hundreds of electrolysis chambers are connected in series and connected to mains power from a transformer that converts the voltage from 110kV or from the supplier's higher voltage factory power supply down to 1-2kV. . High load current is passed through large connecting rods (these bars are usually aluminum plated). The chambers self-heat by the current flowing through them to reach the electrolytic temperature, and the anode modulation system changes the current flowing by raising or lowering the anode rod and thus changing the impedance of the chambers. electrolysis. When needed, a connecting rod is brought into contact to form a bypass (ie, sun connection).
Hall-Heroult . industrial electrolysis chamber
Liquid aluminum is separated by means of a siphon and a suction pump (to avoid the use of pumps and valves subject to high temperatures). Liquid aluminum is transferred into containers or immediately through continuous and heat-resistant pipelines to plating facilities. Metallic aluminum is then either plated to its final shape with other alloying materials or plated into ingots of other impurities to then be sold to smelters for re-smelting.
Whereas, solid cryolite has a higher density than aluminum (solid) at room temperature, liquid aluminum product has a higher density than molten cryolite at around 1000 °C, and thus settles the bottom of the container, which is then periodically sucked out (this prevents the liquid aluminum from being oxidized by the air under the molten cryolite). The top and walls of the container (i.e. the electrolysis chamber) are covered with a solid cryolite shell that acts as insulation. The impedance inside the container (also the electrolytic chamber) is sufficient to keep the cryolite molten.
When alumina has been converted in cryolite, an additional amount of alumina is introduced through a funnel system to maintain the required alumina content in solution. The top of the container does not allow additional alumina to be introduced and so the top of the container must be broken periodically to add alumina to the electrolyte mixture.
The gas released from the electrolysis process is recovered by the gas collection hopper system and released to the outside. Exhaust gas is mainly CO2 generated by cathode (anode) corrosion and hydrogen fluoride (HF) generated from cryolite mixed solution. HF is a highly corrosive gas, especially on glass-coated surfaces, so cranes and heavy equipment used in mining or aluminum smelters need to be covered with all windows and doors. wind with plastic films. HF gas is often treated in adjacent exhaust gas treatment plants, where HF gas is dissolved in water to neutralize the gas's corrosive potential. Particulate matter in the exhaust gas (PM) is also collected and reused through electrostatic methods or filter bags. The remaining component of exhaust gas (mainly CO2) is released into the air, but even if the above emissions are treated properly, it will still contribute to the greenhouse effect.
The intense currents during electrolysis also generate strong magnetic fields and induce hydrodynamic magnetic forces that can dislodge the aluminum from its proper position at the bottom of the tank. This aluminum mixing process, on the one hand, helps the reactions with aluminum take place more completely, but on the other hand, it reduces the purity of the aluminum product (increasing the impurities in the commercial aluminum product) due to the dissimilar materials are completely mixed. According to another technique the electrolytic chamber is operated in what is known as a hydrostatic aluminum bath in which the impurity components either float to the top or sink to the bottom and the pure aluminum remains liquid in the middle.
Aluminum smelters are often located in areas with potential for hydroelectricity, thermal power, renewable energy such as high wind and high economic value. Aluminum smelters using electrolytic technology require a stable power source to operate at maximum capacity and help increase the minimum load so that the demand factor of the power business becomes more stable and less volatile. than; thus can make the overall power generation and transmission system more economical for the end user.
Alumina is the direct source of aluminum in the aluminum production process, but creating the right environment for electrolysis requires another component, and that component is criolite. It is a rare natural fluoride mineral due to its scarcity in its natural form that has been artificially produced. In modern metal production, cryolite is made by mixing hydrofluoric acid with aluminum hydroxide and soda.
So we mined bauxite, produced alumina from it and stockpiled cryolite, and now everything is ready for the final stage: electrolytic reduction to produce aluminum. The miniature area is the heart of an aluminum smelter and it looks very different from the production shops in your typical steel works that make cast iron or steel. The miniature area consists of several rectangular buildings whose length sometimes exceeds 1 km. Inside there are hundreds of cells or pots arranged in rows and connected to the power source through a large cable. The constant voltage at the electrodes of each drop cell ranges from 4 to 6 volts, while amperage can reach 300, 400 KA and more. Electric current is the main productive force in this process.
In each reducing cell, aluminum is produced from alumin through electrolytic reduction. The whole cell is filled with molten cryolite creating a conductive environment at a temperature of 950oC. The bottom of the cell acts as the cathode while the role of the cathode is performed by special carbon cryolite blocks 1.5 meters long and 0.5 meters wide that are lowered into the cell. These blocks look like big hammers.
Every thirty minutes, an automated aluminizing system dumps a portion of fresh alumin into the cell. The current flowing through the cell breaks the bond between the aluminum and oxygen, causing the aluminum to settle to the bottom of the cell and form a layer 10-15 cm deep while the oxygen binds to the carbon in the anodes to form carbon dioxide. .
Two to four times per day, aluminum is extracted from the cell using a special vacuum bucket. A hole is punched in the cryolite shell forming on the surface of the reduction chamber, then a pipe is lowered through the hole. Through this pipe, liquid aluminum is sucked into the bucket, from where all the air is pumped out first. On average, about 1 ton of metal is recovered from each sterilization chamber while a vacuum bucket can hold 4 tons of molten aluminum. After the barrel is full, it will be taken to the foundry.
For every ton of aluminum produced, 280,000 cubic meters of gas are emitted. For this reason, every reduction chamber, regardless of its design, is equipped with a gas removal system that captures the gases emitted during the reduction process and feeds them to the gas treatment plant. Modern dry gas treatment systems use alumina to filter harmful fluoride compounds out of the gas. Therefore, before being used in aluminum production, alumina is first used to treat the exhaust gases released in the previous aluminum production process. So it's a closed loop, in a sense.
The aluminum reduction process requires huge amounts of electricity, so it is important to use renewable energy sources that do not pollute the environment. The most common source of renewable energy is hydroelectric power plants, as they can provide needed energy without polluting the atmosphere. In Russia, for example, 95% of aluminum smelters get their electricity from hydroelectric plants. However, there are places still dominated by coal-fired power generation, for example in China, 93% of aluminum production is produced by coal-fired power plants. When hydroelectric power is used, only 4 tons of carbon dioxide is released into the atmosphere for every ton of aluminum produced, but when coal-fired power is used, the amount of carbon dioxide released per ton of production is five times, or 21 .
The molten aluminum is transported in barrels to the smelter's foundry. At this stage the metal still contains a lot of iron, silicon, copper and other elements. However, even the smallest amount of additive can have a dramatic effect on the properties of aluminum, so in a foundry all additives are removed by melting the aluminum in a furnace. especially at 800oC. As a result, pure aluminum is cast into special molds where it is allowed to solidify.
The smallest aluminum ingots, commonly called pigs, weigh between 6 and 22.5 kg. When customers get their aluminum delivered to them in pigs, they remelt it, add whatever ingredients they need and then re-cast them to the shapes needed for their purposes.
The largest ingots, the 30-ton slabs measuring 11.5 meters in length, are made in special molds buried up to 13 meters deep in the ground. Hot aluminum is poured into a mold like this over a two-hour period, with the slab 'growing' in the mold like an ice cube, just from the bottom up. Once the sheet is cast, it is cooled with water and as soon as the molding is complete, the sheet is ready for shipping. These sheets are then often rolled into thin sheets, which are then used in the manufacture of foil, beverage cans or automotive body panels.
A 7 meter long billet is used for extrusion - this is when the billet is pushed through a hole of the required shape. Extrusion is the process used to make the majority of aluminum products.
In the foundry, not only the aluminum is formed to the required shape, but also the required chemical composition. The problem is that much less pure aluminum is used than aluminum alloys.
Aluminum alloys are made by mixing aluminum with many other metals (so-called alloying elements). Some increase the strength of aluminum, others make it denser, others change its heat transfer properties, and so on. Common alloying elements include boron, iron, silicon, magnesium, manganese, copper, nickel, lead, titanium, chromium, zinc, zirconium, lithium, scandium, silver, and others. In addition, aluminum alloys can include dozens of other alloying elements such as strontium, phosphorus and others, so the total number of possible alloys is impressive. Today more than 100 aluminum alloys are used in industry.
Aluminum manufacturers continuously improve their manufacturing processes to maximize quality while minimizing costs and impact on the environment. Reducing cells have been designed to operate at 400 and 500 KA amperage, older generation reducing cells are being modernized.
One of the most advanced technologies aluminum manufacturers are implementing today is the inert anode process. It's a unique revolutionary process that could allow aluminum manufacturers to stop using carbon anodes altogether. Inert anodes can be used easily, but most importantly, what inert anode-based reductions release to the atmosphere is not carbon dioxide, but pure oxygen. An inert anode call point can produce as much oxygen as 70 hectares of forest. Currently, the inert anode process is being secretly developed and undergoing industrial tests but who knows, maybe in the near future it will turn the aluminum industry into the lungs of our planet. .
Presentation of equipment & technology supplier.
Center of Excellence for Aluminum
You have access to a group of specialists in aluminium that provide independent and unbiased opinion and reviews. Our team is dedicated to projects in aluminium and is organized by key practices. The Center of Excellence includes the following capabilities:
Reduction
You need a partner who understands your business and how it operates. Our extensive knowledge and experience in reduction-technology assessment and selection extends to: mass and energy balances; amperage creep and debottlenecking; time and motion studies; material handling; custom design and optimization of potroom equipment; design and installation of booster circuits; analysis, design, and emergency repair of busbars.
Carbon
You benefit from our experience designing and developing all aspects of the carbon plant. Starting with identifying critical and common problems, we determine throughput restrictions and propose inexpensive equipment upgrades. Our knowledge of the process and industry’s best, available technology means you get solutions to increase production, change anode size to support amperage increases at the potroom and retrofit equipment. We find strategies for upgrading green anode plants, rebuilding anode-baking furnaces, and implement anode-slotting machines and dynamic simulations (ARENA) to establish real production capacities, capital effectiveness and operational efficiency. Last but not least, our integrated engineering team can also address concerns related to the bake furnace firing control system, anode handling equipment, furnace cranes, concrete furnace tub, operating platforms as well as impacts to the fume treatment center and fume ducts to ensure all aspects of your furnace project have captured.
Refractory
Refractories have a major influence on the operating cost and bottom line of any aluminium smelting plant. The initial refractory material cost is significant, but the “full life value” including loss of production and unexpected failures can be more significant. Achieving the best “whole of life value” requires a fully integrated management system. Close cooperation between Our process experts and our refractory technology group allows us to assist with refractory-specific needs across the entire aluminium smelting process including reduction cells, anode bake furnaces, ladles, and aluminium holding furnaces.
We have undertaken numerous anode baking furnace constructions, renovations, and rebuilds which have included design, materials selection, procurement, supply chain logistics, installation, and quality control. Refractory maintenance and rebuild strategies have been developed to reduce the impact on operations and minimize the anode production losses. Refractory experts are experienced in all stages of refractory design and commissioning. We also offer evaluation services including condition assessment, project management, contractor selection, specifications, manufacturing, installation quality control, and ongoing operational support.
Casthouse
With extensive process and equipment know-how across all areas of casthouse operations, you'll have a partner with key expertise in furnace optimization; liquid metal handling and treatment; ingot casting; DC casting, including HDC; and ingot processing. Recent greenfield and brownfield projects include facilities for slab, billet, sow and rod.
Environment
The environment is always a key concern four our clients. Our leading team for environmental technologies devices strategies to reduce or prevent emissions of fluoride, dust and SO2. This is achieved through applying technologies or changing work practices. Our specialists are trained in equipment design and developed process models to anticipate the changes in emissions. We work with all OEMs to bring the right solutions to our clients. We also specialize in fields such as SPL and SO2 scrubbing to assist our clients to make good decisions on managing their air emissions and solid wastes.
High-voltage substations
With services that span conceptual design, feasibility studies, system expansion, and the implementation of greenfield projects, we cater to your distinct needs. From load flows, short-circuits, insulation, and protection coordination, to harmonics studies and site measurements. We have analyzed and implemented more than 50 substation upgrade projects.
Systems and process control
It's big-picture thinking. Our clients come to us for global end-to-end systems-integration services tailored specifically to the aluminum industry. There can be substantial savings and big reductions in the risks associated with integration when a single cohesive team designs, programs, and commissions all aspects of the software systems. Then we up the value again, adding our business functional experts to the mix.
Downstream processing & recycling
After aluminum production, there's still lots to do. We're experienced in brownfield and greenfield developments and optimization: rolling; strip processing; coating and finishing; extrusion; and recycling. Our services extend to automation systems; rolling mill audits; plant studies; training; process analysis; modeling; and cross-the-board optimization.
Issues about Anode anodes need to be discussed in Vietnam Aluminum Corporation:
Buy or make your own.
The preheated carbon anode is a specific type of consumable electrode (anode) designed to melt aluminum through the Hall-Héroult process. During smelting, these carbon anodes are suspended in an electrolytic cell(s) containing an electrolyte, primarily aluminum oxide (Al2O3). In this process, the preheated anode is consumed at a rate of about 450 kg anode per ton of liquid aluminum produced.
With the increased demand for aluminum in many industries, preheated anode prices have trended high over the past three years. Speaking of the market, China has emerged as a global giant in the aluminum sector; and thus one of the important driving forces behind the demand and price of preheated anodes. The Shanghai Metal Market observed that the price of pre-baked anodes in China's domestic market increased by about 620 yuan/ton until January 2017.
SMM allocates benefits to the following three factors:
The prices of coke and coal skyrocketed - the main raw materials of the preheated anode. Crude oil and coke have also made significant strides since November 2016.
China's recent environmental protection activities in Henan and Shandong.
Supply is scarce in China's domestic preheated anode market since January 2017.
China is not only the largest consumer, but also one of the largest manufacturers and suppliers of pre-baked anodes in the world. Companies such as Guangxi Qiangqiang, Jinan Aohai, Jining Carbon, Dezhou Yongxing Carbon and Jinan Wanfang Carbon are all based in China. Looking at the global map, here are the top five prefabricated anode manufacturers in the world:
(Please note, the list below is dynamic and may change according to different market conditions).
1. Aluchemie (Netherlands)
Aluchemie is the world's largest independent manufacturer of custom high-end anodes for the aluminum industry, Aluchemie is part of Rio Tinto, the world's leading aluminum producer. Aluchemie combines advanced technologies with half a century of experience and ongoing training and resource development to create industry-leading preheated anodes. The company ensures that it adheres to a sustainable preheated anode manufacturing method to satisfy demand and be profitable in the long run.
Aluchemie has its headquarters and manufacturing unit in Rotterdam, the Netherlands, although it has state-of-the-art production facilities with a capacity of 450,000 tons of preheated anodes per year.
2. Sunstone (China)
Sunstone Development Co., Ltd specializes in manufacturing and marketing pre-baked carbon anodes both in China as well as worldwide. The company thrives on innovation and continuous improvement of anode quality. To support its commitment to R&D activities, it even opened an independent R&D center in China.
Sunstone owns two pre-baked anode production bases: one in Shandong province in east China and one in Gansu province in northwest China. Sunstone has also expanded its reach globally. It has valuable business partners in Asia, Europe, America, Africa and the Middle East.
https://alcmainapi.azureedge.net/Imagesopt/image/_imgopt_media_imgopt_a57103536ae54fb0ada431a1e4279cf1_0_0.jpg/500/0
3. Rheinfelden (Germany)
Rheinfelden CARBON of the Aluminum Group Rheinfelden, Germany, claims to be the world's first non-toxic electrode patch manufacturer in Europe. Although mainly focused on the production of Soederberg and Electrode Paste (ELPA), Rheinfelden CARBON also manufactures preheated anodes for aluminum smelters.
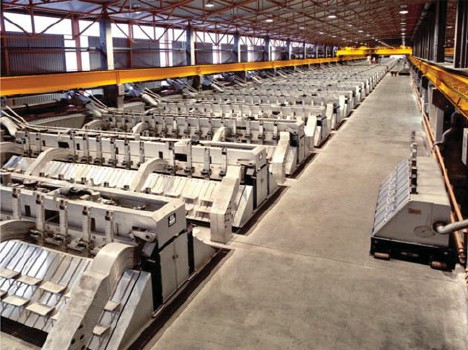
4. Carbonorca (Venezuela)
The state-owned manufacturer of preheated anodes, VG Carbone del Orinoco CA, alias Carbonorca of Venezuela is also the country's most sought-after supplier for aluminum smelters such as CVG Alcasa and CVG-Venalum . The company owns a milling and compacting plant with an annual production capacity of 140,000 tons of green anodes and three furnaces with an annual anode output of 194,000 tons. The preheated carbon anodes manufactured by Carbonorca are sent to reduction plants around the world, including Canada, Egypt, USA, Nigeria, Russia and Tajikistan.
5. Rain CII, Lake Charles (USA)
Rain CII is the leading industrial carbon company in the US With corporate offices in Texas and Connecticut, Rain CII accesses the biggest names in the world aluminum industry with high quality carbon products including preheated anodes. The company has six calciners across the United States and a manufacturing unit in Vishakhapatnam, India. All plants are equipped with rotary kilns, green coke storage facilities, generators with energy recovery and state-of-the-art production and quality control systems, where targeted products are manufactured. for aluminum smelter anode applications.
Hydro, a global aluminum company with integrated operations in the aluminum value chain, opened a trial of anode manufacturing technology in Årdal, Norway, in 2014. Concept of preheated anode manufacturing process Newly created in 2009. This technology is working now. being tested for a potential future industrialization project.
