Production line, tires - Germany
Tire
Solutions for efficient production and excellent products
Maffei Berstorff tires are economical solutions for producing high quality tire components. Through the design of special machines, the system highlights due to:
High throughput in low dimensions and optimal weight tolerance and uniformity
Short retrofitting time during mixing or changing geometry
Waste starting low. Optimized geometric screw for each mixture
Mulitplex extrusion system with 7 extruders
The Maffei Berstorff extrusion system is manufactured with the highest quality and highest output and is equipped with various extruders (GE-SC or GE-W, GE-KS) and sizes. By modular construction, the system configuration, corresponding to the desired cross section, is relatively simple to set up as a double, triple, quadruple, quintuplex and hexaplex unit.
Maffei Berstorff's multiplex systems are formed in piggyback designs to achieve the highest product quality through symmetric material flow in the extruded head. In addition, the compact design offers significant space benefits. An additional feature to meet high quality requirements is the special design of the flow channel in the extruder. They create a very soft and non-invasive transition for the extruded diameter of the screw from a flat, rectangular shape. In addition, the deviation of the volume flow in the channel drops to a minimum.
All process sequences are continuously checked by a monitoring system. Through it, high operational reliability is ensured.
Throughput of up to 10,000 kg / h or approx. 30,000 tires a day are achieved with modern systems.
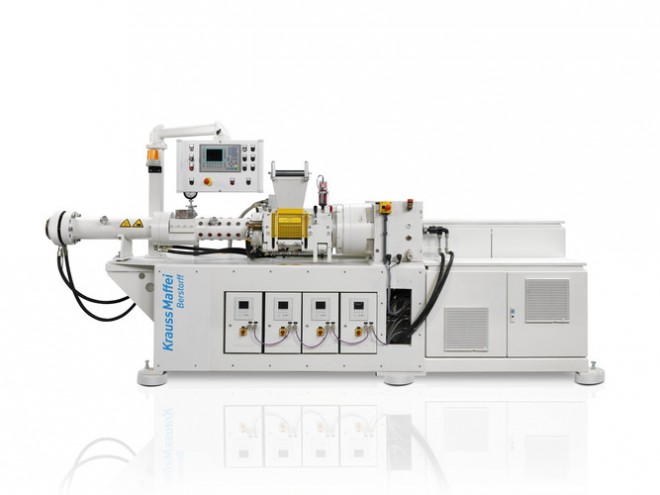
The GE-KS rubber extruder and GE-KS vacuum are all-round machines for many applications. Their versatility and reliability make them truly successful machines in the process. The appeal of battery pincers is further enhanced by the device's extensive range of extras such as automatic battery adjusters, replacement wet sleeves, broken screens and high-performance screws. .
The advanced technology handles a wide spectrum of rubber compounds with different viscosities with just one type of screw, without the need to convert.
We are equipped with extruder Degge-GE EG with a vacuum chamber and the procedure uses battery-barrel technology. The machines offer high output, low melting temperature under injection molding and better dimensional stability for extruded products.
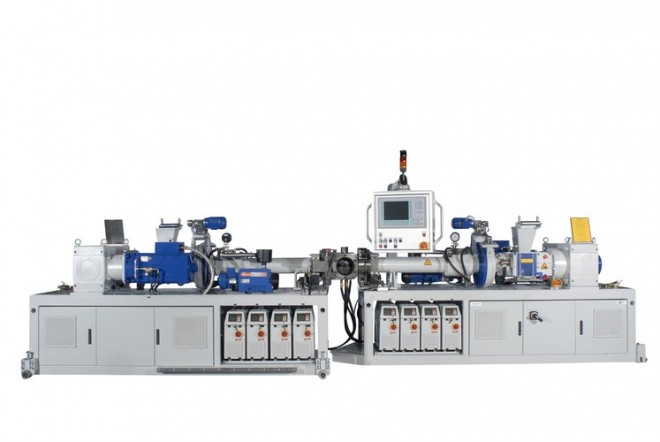
A definite feature of the Maffei Berstorff GE-SC grinder. Pinconvert® is a butterfly unit built in the area near the maximal sheath volume of the sleeve.
It has symmetrically distributed legs around the perimeter that pierce through the sleeve of the sleeve. Can be manually or hydraulically adjustable and allow to reduce the volume of the channel to zero in this area.
Because this allows for production, melting temperatures and uniform performance parameters are influenced and optimized, GE-SC extruders provide you with a guarantee of flexibility and adaptability. can not beat.
We have expanded the options available for the GE-SC's Pinconvert® extruder using specially developed de-gasification systems. The gauge elements are of great importance for extruder models, well, as the extrusion level can be affected by using the penetration depth of the battery before it reaches the deaerator.
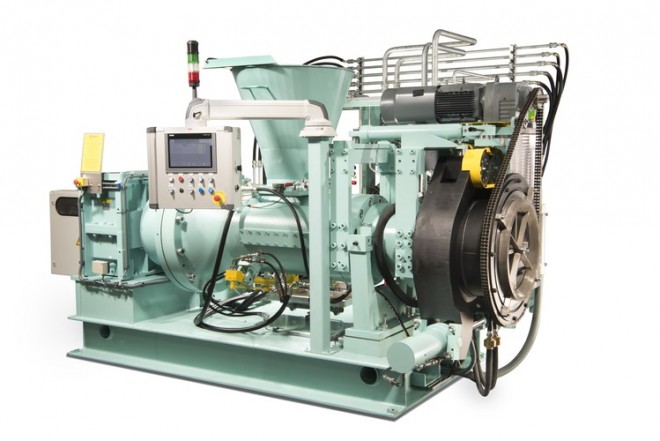
Hot food The extruder of Maffei Berstorff GE-W has proven itself in the production of many types of natural and artificial rubber. They are fed as units downstream of the mills, either continuously with strips or continuously with uncoated rubber rolls. They are made of plastic heated rubber. In addition, they can be arranged as exhausters just below the mixer. In thisform they receive screws with larger diameters and tamping dies as a means to facilitate infeeding.
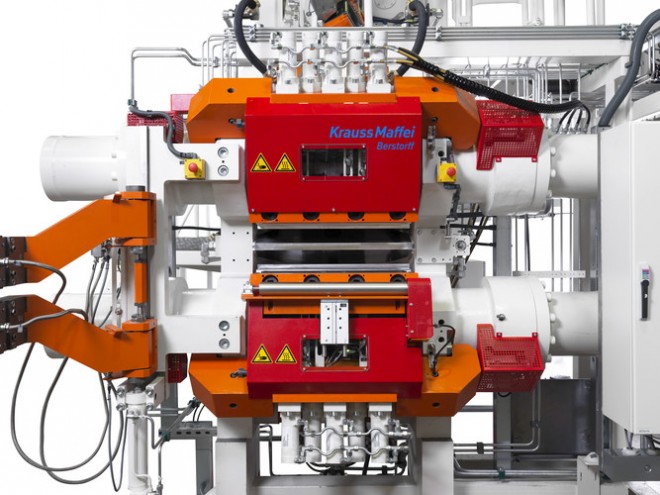
The variety of tires creates complexity, size and change in the production line. The head of each extruded system will become a measure of quality and efficiency in tire production.
To achieve fast repair times in case of frequent change of width while using the same mixture, pressing the Maffei Berstorff die is equipped with a "double wedge wedge". By opening the wedge-shaped wedge, only the last die can be replaced, while the wedge-shaped wedge holds the holder and the bar in the closed position. This minimizes scrap and allows producers to start again quickly.
The top and bottom of the head can be opened separately, to reduce the setting time and the random waste when extruding to change the compound.
Another option to reduce setup time is to use a cassette changer. In this case, two cassettes with the connecting rods and the last bar are used. While one tape is used in the production process, the other can be prepared for the next batch in a changed location by equipping a connecting rod and die.
Working widths up to 550 mm for example: 1 running strip or 2 strips
Work width up to 850 mm for up to 2 strip cars or 2 sub-trailers in one pass
Lock up to 10,000 kN
Connects up to 6 extruders, models and sizes
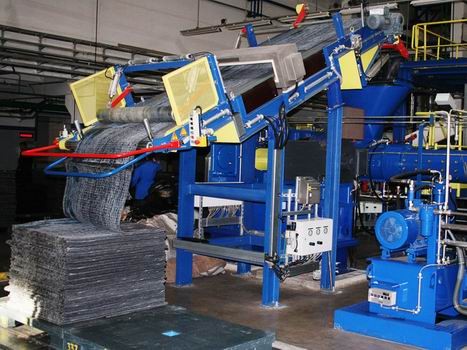
Metal detector
Automatically set the flow rate. Simple maintenance and service. Continuous roller-train rolls and checkweighers for exact weight per meter / piece of measurement. Width measurement equipment, measuring the width of upstream and downstream sections. Cooling. Profile scanners, constantly checking the geometry of records
The length of the measuring device to monitor the length of the tank is accurate
Cut or start / stop cutting for cutting products with cutting quality, accurate length and maximum cutting speed per minute. Rotate to roll operations. To increase adhesion on the coupling surface.
Mark the surface of the lake with colored stripes. Print with identification
Printing with numbers and letters. Seal numbers and letters on the profile surface
Unit for spray cooling or cooling system
Manual track roll
Get the booker automatically
Cassette tape
Conveyor Belt Conveyor
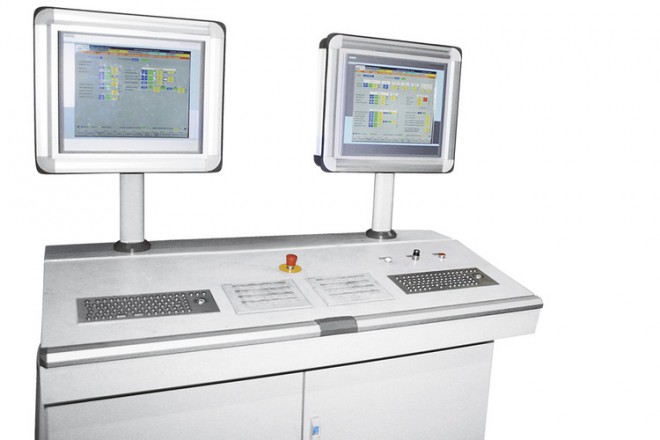
The electrical equipment for the KraussMaffei Berstorff extruded system is modular design based on the most up-to-date technology of the art. Custom configurations can be made in the shortest amount of time without problems.
The extruders are characterized by their microprocessor drives, access to actual digital values and parameter values set via the bus connection. This technology ensures high repetition, precise control and dynamic speed control. These factors are of particular importance for the quality of the extruded profiles. Control software developed by KraussMaffei Berstorff minimizes startup wastes and ensures compliance with measurements and weight balances. of the extrusion mold in the production process. The system continuously measures the weight and the measurement and speed of the screw, the flowing pressure and the melting temperature in individual extruders. In case of deviation of the actual values from the set values, or the parameters of the process are adjusted separately from each other or - depending on the influence on the composition - the parameters of all extruders
The auxiliary drives are equipped with low-maintenance three-phase motors and vector control frequency converters. Non-contact scanning systems such as CCD cameras, ultrasonic sensors and digital rhythm controllers Special numbering allows the transport of stress-free materials. Each system is controlled by a digital software controller, ensuring optimal speed for the following drive.
The automation systems of each machine are networked through TCP / IP and attached to an intuitive display. The operator-friendly image and formula management system clearly provides a plan. flexible production, high product quality, minimal startup waste and short travel times
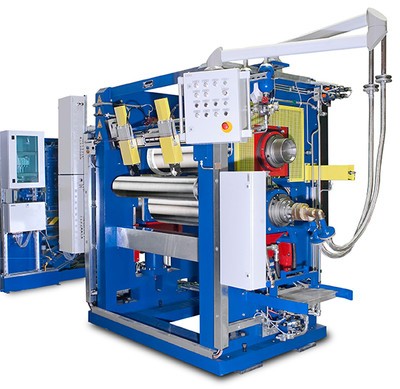
Roller system
Tandem roller system for millimeter work
KraussMaffei Berstorff's roller-head technology offers the perfect combination of cost-effectiveness and accuracy: the lowest degree of deviation in the production of inner linings and chalk or water separators. .
The rubber compound in the extruder is passed through a large injection mold directly onto the coil of the coil. The calender site exactly to the final thickness configuration. The minimum tolerance on the entire surface of the mesh and the uniformity of the optimal mix ensure that the inner lining and filler strips are free of bubbles or pores.
In roller systems the production of rubber membranes, extruders and rolling mills developed by KraussMaffei Berstorff is used exclusively. They are responsible for the excellent product quality with the highest productivity.
Additional technical features at a glance:
The linking mechanism of the extruder and rolling machine during operation
Ability to move extruders to service and refurbish work
Open and close the hydraulic extrusion die for quick cleaning
Automation of all process steps minimizes setup time and increases productivity in roll systems. With central control station and machine control system, the settings for the system can be made convenient and central. The directional navigation system guides the creative process by reducing the set time when changing orders and making it possible to use fewer employees.
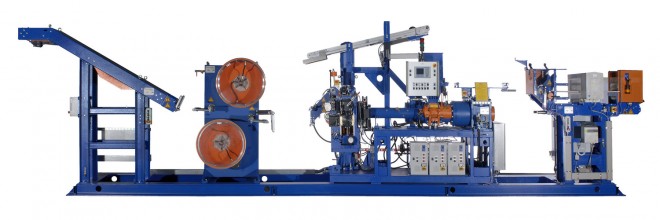
Small roller systems meet the highest requirements for quality, productivity and durability. Whether as a standalone machine or as an integrated system for extruding tire components, such as for extra production.
A small roller system using only extruders, nozzles, and rolls was developed exclusively by KraussMaffei Berstorff. They are responsible for producing accurate filler strips with a wide range of geometries ranging from 0.5 to 4 mm and up to 120 mm in width. Hot rolled coils and special coils are created for the reliability of production. Another advantage is the choice for pruning, always accumulating in the production process, back to production, preservation of materials.
Maffei Berstorff's Calender technology allows for the use of two woven or rubberised wires. Latex replacement rubber and for load bearing tires. Steel wire ensures high stability and high performance.
With the S KraussMaffei Berstorff model provides a comprehensive solution for coating. Custom calender systems are equipped with 4 rolls. Modular structure and various additional features have the highest flexibility and productivity.
The rollers are made of high quality, high grade materials with high precision, high surface quality and hardness. Different heating methods for rollers
Extremely high center system due to special roller system and circulating oil lubrication system of roll system. Hydraulic dip adjustment or quick response time with highest position accuracy, Absolute repetition and fast opening. Tilt and tilt device hydraulic to offset roll deflection
Calender drives for every application intended in absolute quality long-term quality
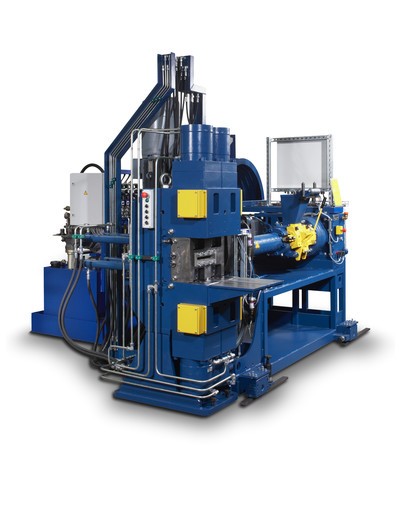
CapStrip system
CapStrip line - the highest quality product and reliable production
The Maffei Berstorff CapStrip Line to produce seamless tapes with nylon or hybrid strings for high speed tires.
The system is designed to be coated with different rubber compounds. 16 strips with 9 threads produced in one pass.
System components:
Creel with 144 rolls to keep the nylon or hybrids
Battery extruding machines for flexible plastic compound rubber and gear pump filling
Gear pumps for uniform output and pressure build
The cross-strap has hydraulic lock to simultaneously cover 16 strips with 9 strings each
Refrigerate the drum
System cumulative
Bolt system with 16 stations
The superior benefits offered by our Cap line give you the quality advantages you are looking for:
Uniform extrusion optimum
Excellent wire coating quality without damaging the wire
Uniform output. Capacity of 40 m / min. 16 strips with 9 strings each in one pass. Short reusable times in case of complex changes.
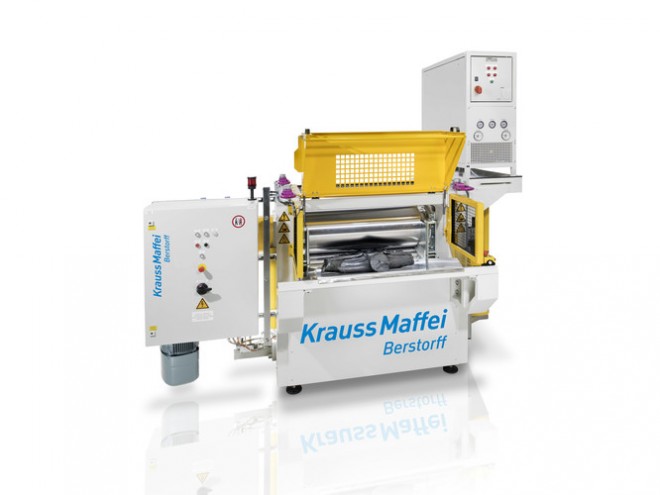
CompoundRework System 1000
For lower cost and high sustainability
Most extruding processes involve the production of recyclable waste, such as residual material in extruders or extruders in the case of composite or machine tools. extruded change. To maximize added value, tire manufacturers try to recycle the scrap by putting it into production.
The CRS 1000 handles rubber waste that has been removed from the flow channels as well as scrap that initially transformed the material into sheets or strips of thickness of 8 mm. This means that 100% of the remaining material can be returned to the manufacturing process.
The CRS 1000 is equipped with two heated coils and a hydraulic adjustable roll space. It can be eaten with residual material of different sizes up to a width of one meter.
Lái xe | <9 kW |
Dấu chân | <4,5 m² |
Cân nặng | ~ 6,5 đến |
Chiều dài cuộn / đường kính | 1000 mm (ø 400 mm) |
Tốc độ | 3,9 m / phút. ~ 3,1 vòng / phút |
Cuộn khoảng cách | 4 - 11 mm |