KER FERRO SYNTHESIS
Production (FeCr / FeMn / SiMn)
Equipment-Technology-Germany
Our international experts specialize in steel mills and submersible furnaces to produce ferro-alloys, silicon, ferrous and non-ferrous alloys. This is where the SMS group in Düsseldorf and Metix in Johannesburg share their know-how for your benefit. Our team at Düsseldorf handles all SAF-related projects for all over the world, except in South Africa. Metix is responsible not only for all of the wet arc electricity plant projects and power melting projects in South Africa, but also for the heating of feed ingredients as well as the homes. Granulator and Cement Production Machine. Paul Wurth provides assistance with refractory design and equipment extraction / baking. We work with you to work together as a team, always finding the best solution possible.
Recent years have been very interesting for the SMS group. That's because of many of the exciting and challenging furnace projects that we do or are currently working on. This includes the world's largest FeNi furnace, the first large scale FeCr production line based on DC technology, silicon plants, FeMn plants, and special alloy furnaces such as FeNb. Read on for our latest reference in the field of ferro alloys, non-ferrous metals, special applications, and hot metal. These references provide the basis for successful melting operations.
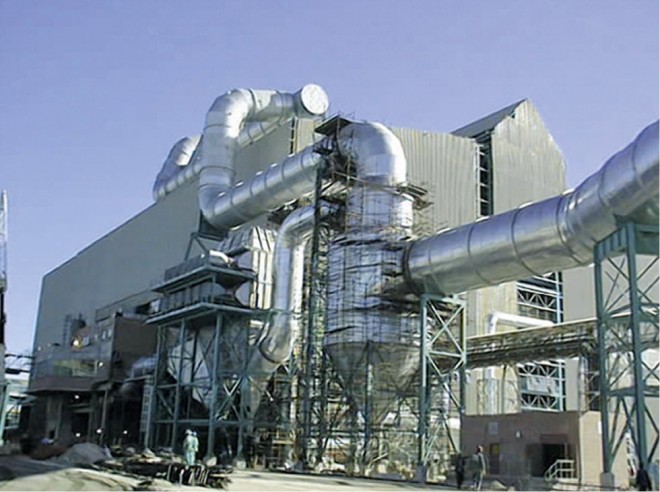
FeCr
The high ferrochrome carbon content is 4-8% carbon. It is commonly used in AOD transformers to produce alloy steel. Due to environmental constraints, ferrochrome is usually produced in closed kilns. ...
FeMn / SiMn
Ferro-manganese is commonly available in the form of high carbon (6-8% C), medium carbon (1 - 4% C), or low carbon (<0.4% C). There are also high-Si alloys (15-20%) called silico-manganese. High carbon manganese carbon
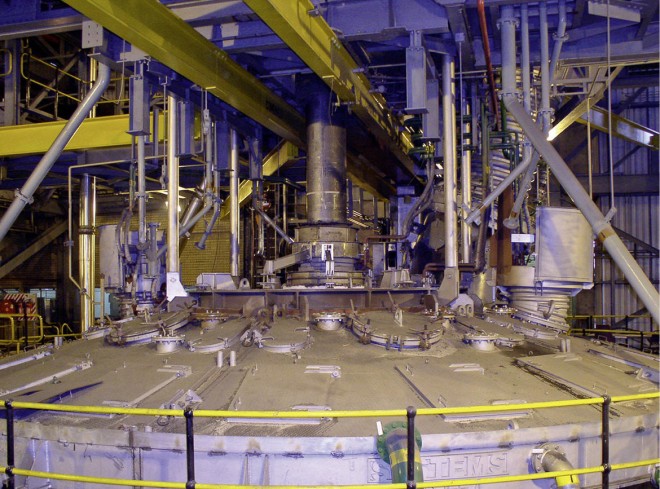
OTHER FRAMEWORK CONDITIONS
Typically, furnaces are open or closed furnaces, AC or DC furnaces. This is a question of available materials, processes selected, and local environmental regulations. Depending on the process and capacity, operators use a rectangular or circular oven.
SMS electrode columns - core devices in each furnace - are renowned for their reliable and efficient performance in all applications. More specifically, it is the current generation of electrode poles because it ensures safe, friendly operation with low energy consumption. That makes them the most modern electrodes on the market. Developed separately by the SMS group, an innovative plain bearings for the lower part of the electrode reduce electrical losses.
Often the selection of side-chilled systems can have a significant effect on the plant's life span. What sets our inherent safety solutions is that they work with the minimum amount of heat needed, saving you energy. They are also suitable for circular as well as rectangular furnaces. In addition, many of our systems include a wide variety of direct and indirect water-cooled solutions, including copper coolers
Synchronous for high power furnace.
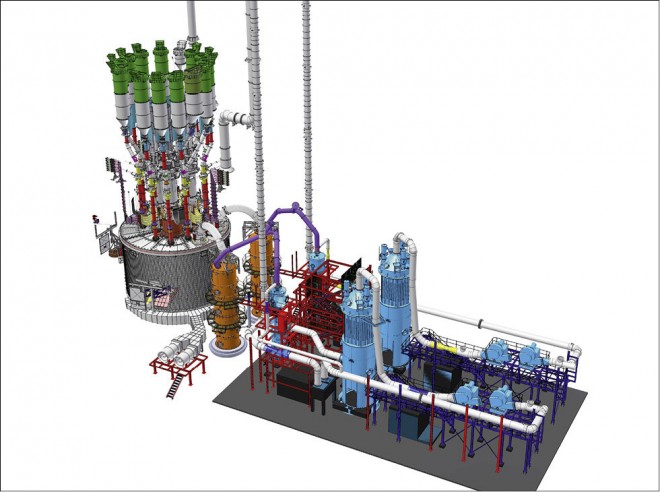
We offer a wide range of roof / oven cover options for different process requirements. The decision here is the maximum temperature that occurs as well as the type of refractory material, steel (water or cooling air), stainless or copper (water-cooled).
New generation DC generators use conventional electrodes. It is also patented by SMS and allows your operators to control and slide the electrodes under full power. That significantly increases the level of production. Also available is an in-house design tool designed to provide curved arc reduction, lasting a lifetime of liner. This DC technology can be used in specific areas such as FeCr, Co, TiO2, and waste recycling.
As a world-class mining technology company, Paul Wurth proposed TMT - Tapping Measuring Technology - a joint venture with Dango & Dienenthal. Equipped with knowledge and heritage, TMT has succeeded in expanding its market position in the past 10 years.
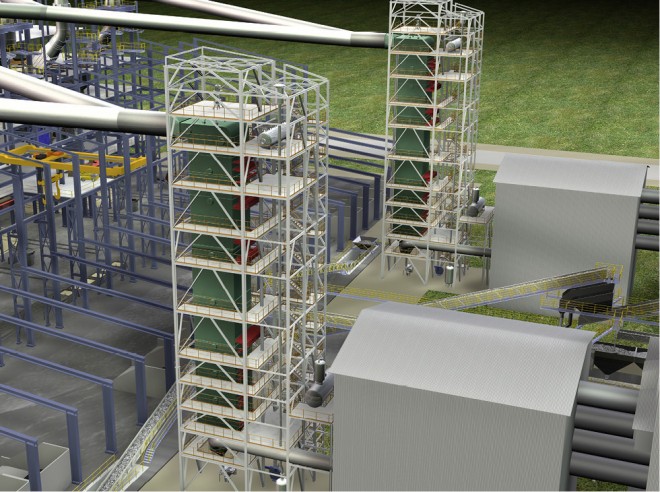
SAF BATTERY INSTALLATION PRODUCTS
Working in South Africa, Metix supplies five of the country's newest cement plants in cooperation with Outotec. The latest version will be available in late 2012 as part of the Xstrata-Merafe Tswelopele project. Included in Tswelopele is a 600,000 t / s sachet and sintering plant made on an EPC basis. It particularly emphasizes our expertise in Cr-ore buildup technology.
There is also a wide range of messaging products to install downstream of the SAF. Available here are advanced equipment for solidification, refining, and metal processing / matte / slag.
Slag systems (static or dynamic, wet and dry) and granular metals
Cast iron and other casting systems for various metals (Fe, Fe alloy, Silicon ...)
Metal / alloy processing equipment
Metal working equipment
Rig screening equipment
Aquarium heating station
Grinding station
Cleaning station
Spraying station
Blown transformer
AOD converter
AOD Transformer
Canceled station
Chemical heaters
Purify water factory
Cooling water system
Heat recovery system
Dust removal and cleaning by gas
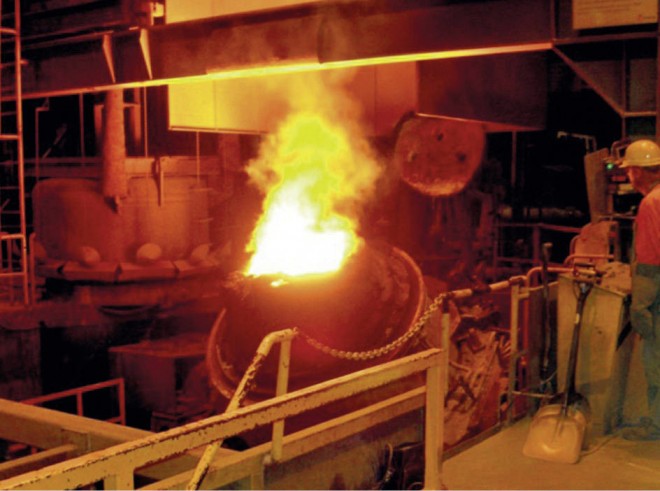
PAUL WURTH IS THE LEADING SUPPLIER FOR CERTIFICATE DISTRIBUTION SYSTEMS
Recognized as the best available technology is their fully automatic wet granule with INBA de-watering followed by condensed steam. This ensures reliable, reliable slag processing and slag production. New on the market is the impact crusher - a solid process by Paul Wurth to produce easy and easy to melt metal particles. The properties of the solid product allow for recycling or chemical processing with less penalties and losses.
In order to benefit both you and the environment, we have developed initiatives in energy recovery, water treatment, air pollution control, by-products and recycling technologies as well as energy management services. Our solutions combine sustainability and economic performance with our Ecoplants brand.
Our cleaning department focuses on making our plants environmentally friendly and keeping your workplace clean. It is based on the in-depth experience of our entire product portfolio. This system includes dust and gas cleaning systems for submersible furnaces, arc furnaces, BOFs, and other equipment used in the steel and metal industries. The SMS Group provides dry and wet cleaning systems as well as pre-vacuum cleaners. To date, we have been involved in the construction of over 35 gas purification plants for the submerged kiln.
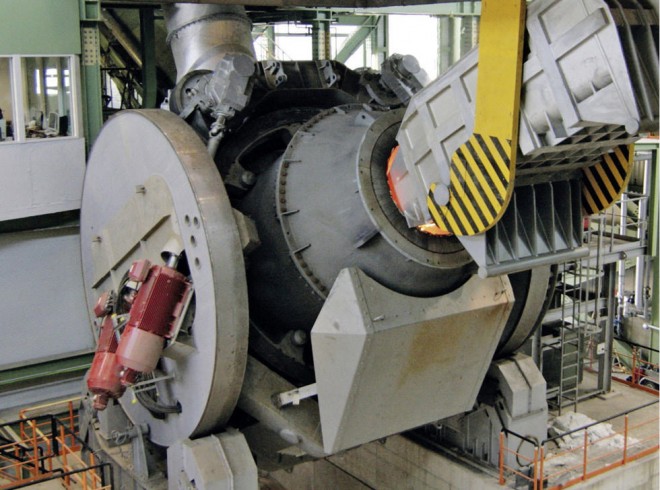
AIR CLEANING
When cleaning the gas, we are specialists, with overall systems and secondary education to protect the environment and keep the workplace clean. These include
• Dry cleaning system
• Wet cleaning solution
• Electronic condensate (ESP)
• Hybrid system (combined wet cleaning and ESP)
The hybrid system is an ideal investment solution for plant upgrades where conventional filters no longer meet environmental standards.
More often than not, the process determines how much electricity a cooker consumes. We significantly improved energy use by connecting kilns to energy recovery systems. This ensures that the hot gas from the kiln is recovered in the ideal waste boiler, while the gas boiler processes heat and chemical recovery reasonably from the boiler. This also reduces your carbon footprint.
You can count on a range of SMS technology for iron metallurgy, with focus on FeNi, FeCr, FeMn and other alloys. Our system has a furnace with auxiliary equipment or special switch. We draw a long history of converting technology to give you the best solution today.
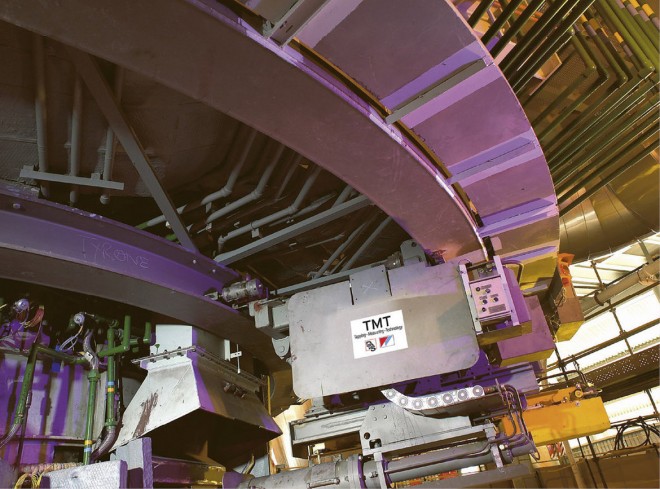
VARIOUS SYSTEMS FOR OPTIMUM OPERATIONS
You can choose from these converters:
Conventional BOF converter for FeNi
AOD converters for MC FeMn and MC FeCr
X-Melt Vacuum Transformer
It is important that materials are handled, handled, and conditions in such a way as to ensure optimum oven operation.
This is where the SMS group offers you many different systems such as:
Unloading trucks, trains and ships
Warehouse systems, such as loading and unloading systems
Preparation of materials, such as washing, sorting, screening, drying, agglomeration and separation
Conveyor system for all facilities
Most applications involve the casting of SAFs into solids before further processing to meet the requirements of the product. This is our range of systems for die-casting products:
Grinding, grinding and crushing plants
Classification, screening, and calibration systems
Coagulation and lagoon facilities
Packaging facilities and queuing system
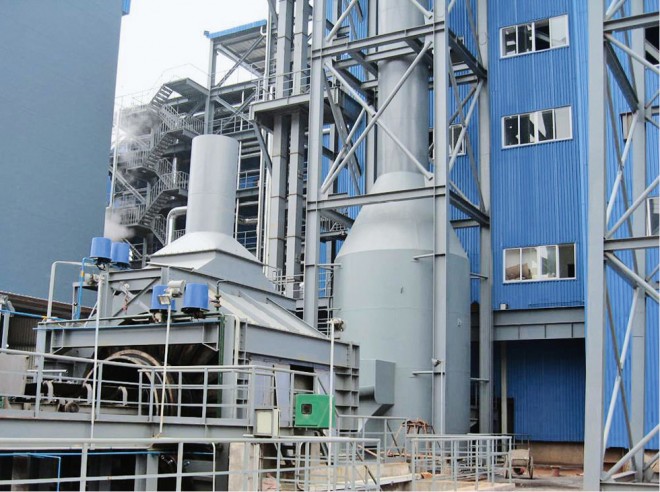