Plant, sintered ore, in steel-Luxembourg complex
Supplying equipment and transferring production technology
Mix the ingredients and put the ingredients in the oven
Equipped for the most challenging material characteristics
In order to achieve high productivity and stable quality, the excellent consistency and high permeability of the sinter raw material must be obtained from the start. In response to challenging input materials, Luxembourg offers tailor-made solutions for blending and finishing. We recommend, for example, mixing a horizontal or vertical mixer with a drum kit or using a horizontal or vertical mixer with an intensive nuclining - depending on the type of material the operator is using. Material and space characteristics are available for mixing pre / mixed yards.
In addition, we provide advanced systems for mixing sub-materials into sinter fibers, designed to reduce material compression and to ensure separation during the discharge process for optimum ignition.
Working closely with sinter plant operators as well as various laboratories to perform specific mixing / nodulation tests helps us find the most suitable solution for the quality of iron ore. and quality.
Furnace.
Improved design to improve productivity
Luxembourg's design of the ignition hood with a vertical burner arrangement enhances the sintering process. Compared with horizontal lids, the configuration of the vertical burner has many advantages with direct effect on plant productivity. Its compact design increases effective sintering area and reduces specific fuel consumption. An enhanced temperature profile and control allows the reduction of the production of cement crystallites, which directly affects the net production and consumption of solid fuels. Yarn production is enhanced by longer fiber lengths in the case of a traditional muffler replacement, reduced start-up times and reduced maintenance. Heat efficiency is optimized, resulting in lower fuel consumption. Final,
Processed output.
Strong and low maintenance equipment
Hot and cold sintering and screening require heavy equipment but only reduce maintenance. Luxembourg can provide cement grinding machines with specially designed worn parts, which increase life expectancy compared to traditional designs.
Paul Wurth's portfolio of output materials includes hot and cold milling equipment, multi-layered sorting and sintering sampling systems.
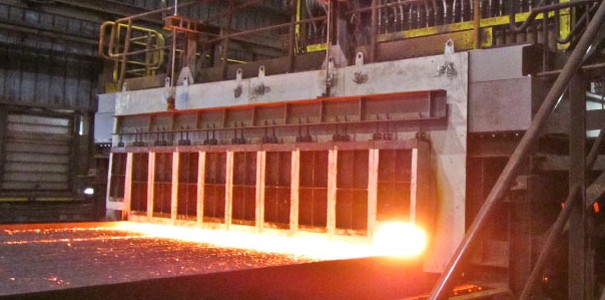
The system is cool.
Flexible cooling technology with heat recovery solutions
Sinter coolers are often the bottleneck of cement production, with outdated technology leading to low productivity and high operating and maintenance costs. This is countered by two types of coolers developed and supplied by Luxembourg: the Annular Cooler and the Cooler Shaft.
The classic design of the annular cooler has been completely revised and now basically consists of a rigid round frame structure for easy and durable material center. Additional features, such as reliable sealing systems, lead to low operating costs and increased air sealing.
Luxembourg has successfully transformed the axial cooling equipment into a patented, patented airflow design, extracting 100% of the heat in the sintering process for high efficiency heat recovery processes. . With its compact design, the current rotary cooler allows longer time of coarse adhesive in the cooler, resulting in better cooling performance and reduced dust emissions.
All Paul Wurth radiators are perfectly suited to any type of heat recovery, which can be tailored to the needs of each customer.
Providing specialized services
In line with the trend in the production of fine ores and concentrates, the increasing demand of blast furnace operators and factories reduces direct high-quality materials as well as general production requirements. With the environment and cost savings, Luxembourg is providing the services selected for the packaging of iron ore and similar materials.
The focus of the activity is on optimizing current operations and includes research to debug, increase capacity, reduce energy, improve quality, and reduce emissions.
Shutdown monitoring, especially for steel mills, operational support and additional advice for pelleting services.
Exhaust gas treatment.
Provide environmental safety
Luxembourg proposes a range of technologies from reducing emissions through recirculation of exhaust gases to cement plants to tailor-made exhaust gas treatment systems. Here, our solutions include simple auxiliary sprinkler systems from the upstream of the ESP filter to the entrained flow hoods combined with specially designed bag filters for efficiency. maximum. These technologies allow simultaneous removal of acidic components (HF, HCl, SOx ...) dioxins, furans and dust. Similarly, NOx and CO reduction plants may also be adapted to meet local constraints and regulations.
These custom and economical solutions ensure that cement plants and pellets operate under increasingly tight environmental regulations with the lowest operating costs possible and without compromising performance. the result of the accumulation process.
Process automation and control.
Expert system for plastering operations and fine grinding machines
SINTERXpert ™ is Luxembourg's Level-2 integrated system for control and optimization of processes, with online expert rules for advanced decomposition plant operations. The powerful models and features associated with field measuring devices help the customer in accomplishing his or her operational goals and optimizing the complete sintering process.
The system can integrate the Computing Model, Online Balance Online, HMI, Trends & Reports, Firefighter Tracking and Online Expert Rule with various control modules. .
The development of two-stage process control systems for pelletizing plants, including the entire process from mixing the material to the granulation, permeation and screening, and providing an interface with a melting furnace and / or a direct reduction furnace, complete the offer.