Factory, steel production, blast furnace. Luxembourg Technology.
Equipment supply and technology transfer
INTRODUCE
Leading in steelmaking technology!
Luxembourg and iron production professionals are proud to offer their modern technologies to the furnaces around the world! Most of the medium and large reactors in the world now incorporate Paul Wurth technology. Now many smaller size ovens benefit from Paul Wurth's technology too!
Our products and services include a full range of blast furnace projects, from new complete manufacturing plants, modern and related furnaces, new and upgraded equipment, plant automation systems. and process control, engineering design services through maintenance of equipment and parts. We provide system design and operation consultancy for operation and maintenance of blast furnace.
The benefits to customers may include:
Factory capacity is higher
Higher unit yields
The plant has high reliability and availability
Improved hot and stable metal quality
Low energy consumption
Reduce operating costs
Improve factory hygiene
Improved environmental performance
Improve plant safety
The campaign life is longer
Access to the innovation and continuous development of Luxembourg
BUILDING AND MODERN LARGE CHEMICAL
The solution is proven along with the latest technology.
Luxembourg has a reputation as a pioneer in Burning Furnace Engineering - to develop new plants as well as to upgrade existing ones. 230 reference projects around the world are witnessing unique capabilities and the entire plant.
The modern Luxembourg furnace combines proven solutions with the latest and the latest developments to maximize the benefits of the project - capital and operating costs, project implementation, operation, reliability, availability, safety, plant sanitation, environmental compliance, and life.
We work closely with our customers to develop optimal solutions - whether for a new furnace or for relining or rebuilding an existing unit. We work closely with our subcontractors and construction companies to minimize the impact of the main work on ongoing activities, uptime or construction and cost optimization for our guests. row.
Our continuous improvement philosophy ensures that our clients receive the most advanced technology and proven solutions for the technical and commercial success of the project.
MATERIAL SUPPLY SYSTEM
Luxembourg can provide state-of-the-art solutions for workshops and associated charging systems, including all equipment and facilities for storage, weighing, screening, transportation and transportation.
The warehouse designed by Luxembourg is characterized by: high flexibility in batch processing and sequential charging options,
Full battery backup capacity, high filter efficiency and reduced minimum burden burden through a limited switching point.
For all system load design, process and operation simulations are performed. Similarly, the combination of effective disinfection systems is considered in every case to meet environmental regulations.
CÔNG NGHỆ LÒ ĐỐT LỚN NHẤT BLAST FURNACE
Kể từ khi ứng dụng công nghiệp thành công đầu tiên của BLT ® vào năm 1972, Luxembourg đã phát triển một hệ thống Pin Bell nhỏ Top ® lớn cho bất kỳ quy mô lò cao nào, đáp ứng yêu cầu của khách hàng về phân phối gánh nặng và phân chia gánh nặng linh hoạt, trong khi vẫn phù hợp với ngân sách của họ . Kiến thức của chúng tôi thu được từ khoảng 700 cài đặt, kết hợp với kinh nghiệm hoạt động của khách hàng và quá trình phát triển sản phẩm theo quá trình của chúng tôi, tất cả được đóng gói thành một công nghệ sạc độc đáo - đó là những gì tạo nên tiêu chuẩn trong việc chế tạo sắt thép.
Việc áp dụng hệ thống tính phí Bell Less Top mang lại những lợi ích sau:
Cải tiến hoạt động ổn định lò & hiệu quả dẫn đến kiểm soát hóa học kim loại nóng nóng tốt hơn;
Tăng năng suất lò;
Giảm chi phí vận hành do giảm tiêu thụ coke và tỷ lệ PCI có thể đạt được cao hơn;
Cuộc đời chiến dịch dài hơn nhờ giảm tải nhiệt của lò sưởi;
Bảo trì thiết bị hạn chế, dễ dàng và nhanh chóng bảo trì.
BLAST FURNACE DESIGN
Proper design of the appropriate furnace is reliable operation, metallurgical efficiency, high productivity durability and longevity of the operation.
For high power turnkey installations as well as refurbishment of the plant, the modern furnace designs of Luxembourg are based on the concept of free units with the surrounding building structure, Access the furnace entrance and support furnace exhaust system. Using powerful simulation tools to optimize the burden and flow of gases, Luxembourg designs the appropriate furnace to consider potential materials and operating conditions for the furnace throughout the campaign. Serious consideration is given during the design phase to ensure quick and accurate construction calculations.
Integral shell features, cooling elements and refractory, the global solution designed by Luxembourg ensures the full operation of the plant's balance.
LOSE AND LOSS
With years of experience in lining kilns and proven know-how in the definition of furnace definition and cooling, Luxembourg offers complete solutions from the bottom and the fireplace to the top of the blast furnace.
Based on the extensive knowledge demonstrated in more than 250 blast furnace projects, Luxembourg provides refractory design, material supply and construction supervision for the entire blast furnace.
Effective cooling is required to balance the heat load and wear associated with the inner liner of the furnace. Provided with our copper and cast chillers for any area of the blast furnace, our optimized and secondary optimum cooling system operates on over 50 large furnaces (117 documents reference) around the world. To ensure high availability, long service life and reduced operating costs, Luxembourg uses circular cooling circuits primarily by forced coil.
Advantages:
Low water consumption;
Low power consumption;
Low maintenance costs;
Non-corrosive or obstructed piping and cooling elements;
Detection of leakage sensitivity;
Highest operational safety.
ELECTRICITY DEVELOPMENT AND HEAT RECOVERY
Luxembourg proposes the best technology for the construction of turnkey furnace systems with internal and external combustion chambers as well as repairs of all types.
The benefits of our solutions are:
uninterrupted oven operation for many years;
high energy efficiency;
maintenance free system;
low emission;
optimal use of available space;
Long-established concepts against erosion of corrosive stress.
By reclaiming the heat from the furnace gas while heating the stove and using this heat to preheat the combustion air and furnace, the overall thermal efficiency of the hot stove can be improved to save energy. Significant and optimized operating costs. The heat recovery systems provided by Luxembourg based on heat pipe technology and the use of thermal oil are medium.
Luxembourg designed Hot Wire and Tube to bustle to handle system movements and residual expansion to provide trouble free operation. A master mixer or individual mixer can be combined.
Our portfolio also includes an entire set of valves used for hot-flash applications.
The Paul Wurth Tuyere collection, which is applied on more than 150 blast furnaces, is designed for long life, easy transport, low maintenance and no noise pollution. The bellows designed by Luxembourg can be easily adapted to accept secondary fuel injection.
COOLING MILLING
Reliable, efficient and accurate dispersing of auxiliaries is essential for the operation of the blast furnace. Paul Wurth is involved in the development and application of all types of degassers, liquids and liquids through hot spray pipes. Luxembourg has been involved in the pioneering development of Coagulating Technology (PCI) since the early 1980s; Today, almost 70 large Blast Kilns worldwide are operating with our PCI systems.
Luxembourg of the Basic Types of PCI Systems
Personal flow control: This configuration provides the highest coal transport precision for each sputtering bush.
Global Flow Control with Static Distributors: A static separator followed by flow balancing in individual feed lines is optimized for length that allows excellent control of the distribution of coal for each. syringe.
Global Flow Control with Dynamic Distributors: Instead of using flow velocity controllers in individual feed lines, this configuration uses direct flow measurement and flow control valves. GRIPSKO ® Paul Luxembourg to achieve higher coal delivery accuracy.
Improvement of coal combustion / burning in Tuyeres: Luxembourg provides oxygencoal lance and coal heating technologies to improve the efficiency and capacity of coal introduced into the furnace process.
Stone kiln and drying
Luxembourg designs and supplies coal grinders and coal grinders to convert raw coal into crushed coal. The selection of hot gas heaters, vertical mills and efficient filtration technology, all provided by reputable system suppliers in their field, makes the Luxembourg mill and dryer become An ideal technology unit for PCI operations
ENERGY RECEPTION
The high efficiency gas cleaning system is vital to the reliable operation and longevity of high-temperature hot water treatment systems and steam production facilities, and enables operators to meet related pollution control standards.
We design and supply a complete range of gas cleaning systems, gas distribution equipment and processes designed to achieve the highest cleaning efficiency, safety and reliability and provide protection to the environment. the best possible. With over 130 references around the world, Luxembourg offers turnkey plants and core components to clean the top gas of the blast furnace, including
Axial Cyclone
Compact design; Abrasion-resistant membrane optimizes system life;
Easy adaptation to existing plants (no downforce support). Venturi holes. High separation efficiency with minimal pressure loss. personal temperament (local).
Demister Top Turbine Gas Energy Recovery
The efficiency and accuracy of dust extraction results in a high recycling rate of iron-based byproducts,
RESTORATION OF TOP ENERGY
Mitigating the environmental impact of technology solutions is one of Paul Wurth's daily challenges. In the field of blast furnace, Luxembourg is continuing to exploit the energy saving potential of the BF process and continue to optimize high efficiency (TRT) high efficiency recovery turbines.
By leading the blast furnace offshore through an expansion turbine installed below the gas purifier, the kinetic energy contained in the pressures of the blast furnace gas is converted into electricity. For high-pressure blast furnaces, the recovery of gas results in significant electricity savings and significantly reduces CO 2 emissions.
BLAST BLOOD PUMP
For decades, Paul Wurth has been designing and supplying specialized valves and dialysis equipment for various applications in the blast furnace process. Luxembourg designs valves to meet and exceed the harshest operating conditions expected in blast furnace operation. They are designed for long life, high reliability and easy maintenance.
This line of products is constantly evolving, so new features and components are tailored to the latest application, quality and service requirements.
The Luxembourg Valve family includes:
Cooling Valves (furnace burners and semi-clean gas)
Pressure valve and pressure drop of the pressure of the furnace
BF Main Gas Shut-off / Valves isolation
Vacuum pump (GRITZKO ®) Valves (for vacuum cleaners and cyclones)
GRIZKO ® (compressed air flow control valves) (for grinding and other materials)
Van Goggle (for positive isolation of gas pipelines)
Van Septum (to reduce the pressure of clean BF gas)
Van Snort (to control BF explosion)
Gate, butterfly, double eccentric and three lever valves to isolate and control BF hot heater plants and other applications, including:
Cold Blast - Mixing - Heat - Explosion - Venting - Gas - Air - Chimney / Exhaust - Waste Heat Recovery - Isolation, Safety & Drafting - TRT.
AUTOMATIC SYSTEM & LIGHT SYSTEM
The efficient operation of modern blast furnaces requires high levels of automation along with computerized monitoring and control systems.
For each Luxembourg Technology / Equipment, we provide Level 1 Automation (PLC and HMI). A team of experts has developed advanced control procedures for any specific process.
In addition to the general automation functions, advanced functionality is included in Luxembourg's Auto Level 2 solutions.
Paul Wurth's BFXpert ™ Blast Furnace Blast Furnace combines process models and expert systems to analyze data and optimize processes. It supports BF operators in optimizing the stability and cost of hot metal production, while being supported by a knowledge-based system. Process data processing supports reporting of performance indicators and production data.
Designed for operator support and process optimization, BFXpert can contribute significantly to energy efficiency and cost savings.
Similar specific systems are available for related processes such as coking and sintering, thus permitting optimization of the whole plant.
DRAGON DISEASE (TMT *)
With decades of development, design and delivery of advanced blast furnace exploration, Luxembourg has incorporated the design know-how with Dango & Dienenthal in TMT - Tapping Measuring Technology. Luxembourg works with colleagues at TMT and with clients to make the best combination of transducers and instrumentation to accurately track and control the blast furnace process.
Reliable exploration is important to support data processing, furnace process models and furnace operation monitoring systems.
TMT probes include:
Chain detector
Profilemeter / 3DTopScan
TMT Soma - a system for measuring the Acoustic gas head temperature for blast furnaces
On the gas probe burner and temperature
Conductor collision
The vertical probe reduces
Check gas probe & temperature in burdens
Scanning probe
Tuyere exploration
Torpedo level detector
CASTHOUSE LAYOUT & EQUIPMENT (TMT *)
Luxembourg has extensive experience in designing modern, high-performance homes - whether new or modernized existing plants.
The flat layout as well as all design features ensure reliable operation and flexibility, easy maintenance and best safety conditions. Technically, modern BFD systems are available to help BF's operations comply with the most stringent environmental regulations.
Luxembourg proposes and uses world class factory equipment from TMT - Tapping Measuring Technology, a joint venture of Dango & Dienenthal and Luxembourg. All of TMT's exclusive contractor equipment include:
Hydraulic guns;
Drill boring (hydraulic or pneumatic operation, bar dipping bar);
Filler gun;
Automatic drilling machine;
Beat Jack;
Sampling equipment;
Runner cover manipulators;
Tilting Runners & Drives;
Torpedo level measurement system.
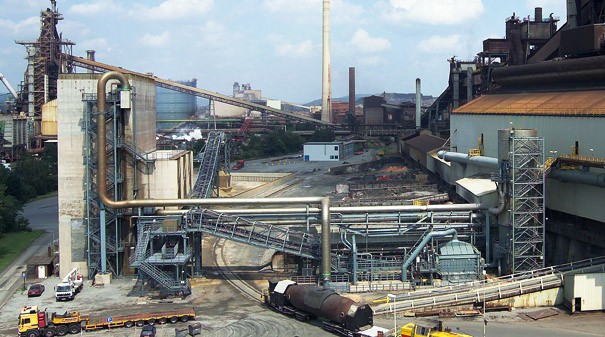
DISTRIBUTION OF BLAST REFRIGERATION
Slag treatment is an important aspect of modern slaughter operations. Today, blast furnace slag is a viable product (marble slag is used as a CO2-friendly replacement for cement) rather than a difficult and expensive waste. Luxembourg has developed the INBA ® slag process, incorporating our exclusive INBA dewatering drum. With about 300 reference materials, this is the most popular and effective means of processing large slag ovens in the world today. This process is very flexible; and the compact sub can be applied to any furnace configuration. Granulating, dewatering and slag storage can be done next to the furnace or can be divided to fit the available plant space or logistics. Modern condensing concepts and closed water circuits ensure effective environmental control. INBA system with steam condenser is officially recognized as Best Available Technology (BAT).
Customer benefits:
Very compact design for maximum flexibility in layout
Continuous filtering and slurry removal of wastewater
Low quality content in closed water
High reliability
Measure the flow of slag flow
Reduce emissions and control air pollution
Low investment, operation and maintenance costs
The thin body on the drum
RUBBER MACHINE
Paul Wurth supplies modern pig casting machines for the latest generation of molding, process control and monitoring. Our technology reduces maintenance and installation time as well as increases production and control.
All our machines are built based on a modular type building design. They can be a single thread or double thread machine with different designs depending on the method of pouring. The size and rigidity of the wheels are based on the payload per hour and the size of the wheel.
Paul Wurth can consider various designs in standard design along with a complete automation package and includes a number of optional features.
Main advantages:
Highly available;
Reduced maintenance requirements due to optimized component design;
Standard components for fast exchange and changeability;
Optimal water;
Wide temperature monitoring;
Fully automatic operation machine;
Innovative solutions to meet stringent environmental requirements.
MIDREX MEMORY
Paul Wurth has taken an important step towards becoming a complete supplier of all iron and steel production processes by 2014 when signing a construction license agreement with Kobe Steel in Japan. As a result, Paul Wurth is able to provide direct iron-based ironreaking plants based on Midrex® as part of its portfolio.
Direct reduction process Midrex ® is the industry's most efficient technology for producing high quality direct-reduced iron (DRI) products, accounting for about 60% of the world's annual output. DRI and its derivatives, including hot cast iron (HBI), are pure iron materials commonly used in steel manufacturing applications. Demand for global DRI products is increasing the interest of the world's direct reduction factories.
New applications to meet different industrial needs:
Midrex NG ™ is a configuration of the Midrex ® process using natural gas, considered the cleanest fuel. Through the use of the patented Midrex® enhancements, this cost-effective process reduces the amount of iron available for the reduction of iron ore occurring in the Midrex® shaft.
MXCOL ® uses synthetic gas, or synthesis gas, from glass making or coal gasification to produce DRI in the Midrex ® process.
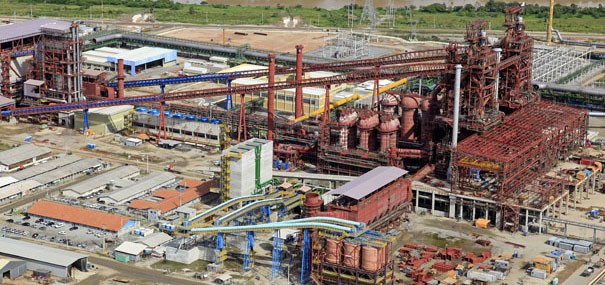