Factory, Recycling, Production, Copper - Austria
Austria - Supply, production line and technology.
Furnace system for copper industry
ANDRITZ provides conversion, melting and refining furnaces for primary and secondary production, as well as for the copper processing industry .ANDRITZ Maerz supplies turnkey furnace systems for copper and metallurgical metallurgy precious.
Directly to the wire
Direct-To-Wire is a filter technology that optimizes the production of "highly refined copper coils" (FRHC coils) for the production of copper scrap rods. Copper FRHC liquid can be used directly in the process of casting and rolling steel wire. This technology is based on the long experience of ANDRITZ metal in furnace construction and, due to its versatility, can be installed in existing or new copper rod plants. Depending on the required production capacity, Direct-To-Wire can be made with three different furnace concepts.
ANDRITZ METALS concept furnace with Direct-To-Wire technology 240 to 600 t / d: efficient furnace for melting combined with two drum type furnaces for filtration and casting
40 to 300 t / d: Flexible tilt furnace for melting, refining and casting, can be expanded by second furnace, 20 to 30 t / d: Blast furnace for melting, refining and casting, expansion By second furnace for minimum investment. To achieve optimum performance and cycle time, all ANDRITZ METALS furnaces are equipped with high-pressure and high-pressure hoses in addition to other technical advantages.
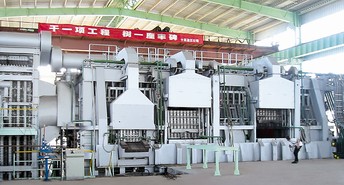
Kiln type drum
Vacuum boilers are mainly used to refine co-liquid from upstream refining furnaces in primary and secondary metallurgy. They can be applied as anode furnace and refining furnace for copper rods or as Pierce Smith converter. The drum type furnace is also available in a design for handling solid waste input. Capacity from 20 to 630 tons has been made.
Advantages of drum furnace
Fast and efficient refining. Advanced and proven refining technology with submersible submerging tools. Solid and liquid inputs can be processed
The precise dosage in the casting process by rotating the control of the vessel furnace
Tuyere technology for gas and liquid degasser. Optimized logistics in the plant due to the simultaneous operation of two or more drum type drums.
Refining package
Technical packages and equipment to modernize and optimize existing plants; These packages are intended to increase metal yield and metallurgical efficiency, and optimize energy usage by improving processing technology.
Package refinements include
Tune up the system
Combustion system with or without oxygen
Nitrogen cleaning system
FEM calculation
CFD calculation
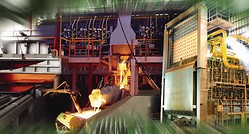
Advantages
Higher copper output
High-grade copper production
Shorten processing time due to higher processing efficiency
Enhanced bath movement due to the special stirring elements arranged in the oven
Optimizes download cancellation routines due to specially arranged options
Better heat utilization due to optimal heat transfer
Furnaces and ovens
or the effective melting of the various copper qualities, ANDRITZ Maerz provides furnace shafts and heaters. The heater enables the melting of copper cathodes, anode residues, and high-grade copper scrap with very high energy efficiency. High efficiency is achieved thanks to the one-burner control system and optimal furnace geometry. The material is charged to the shaft with a bypass hoist. The burner is mounted around the lower shaft, providing the molten energy. Emissions move upward through the shaft to pre-heat solid waste at the top of the shaft. Copper liquids can be brought to the next step by means of a cooker or washing machine.
The furnace is equipped with an additional fireplace to keep, reduce, and handle additional copper. Therefore, low quality scrap can also be used. The molten copper is passed through a washing machine to refine the furnace. Production capacity up to 90 t / h can be achieved.
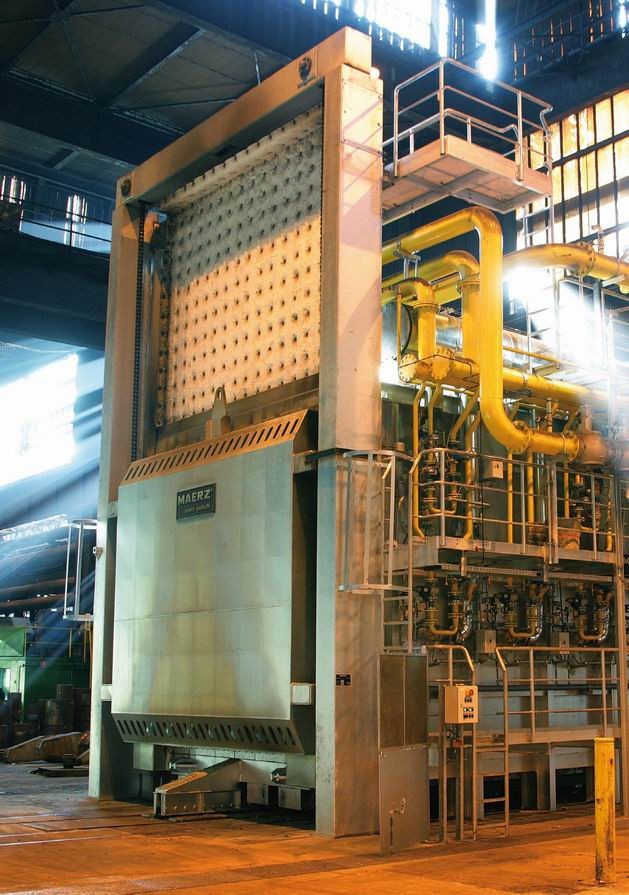
Advantages of kilns and furnaces
The melting fast and continuous
Optimal thermal performance
Preheating of waste materials by upstream extraneous gas
Apply for different scrap qualities
Sound reflector
ANDRITZ METALS has been proven for the melting and refining of large quantities of low-grade scrap in a single unit. Capacity has been made from 50 to 500 tons.
Advantages of leaning reflex
The melting fast and continuous
Rapid, efficient melting of copper due to optimized burning technology
Quick charge scrap
High heat transfer rate for shaving and bathing
High quality copper output due to strict monitoring process and efficient process
Quick and effective reaction of copper impurities due to the direct action of the reaction agent through wet weather particles
The tilt system allows for flexible operation in charge / reduction and casting
Fast reproduction process
Easy, reduced maintenance
Ease of operation reduces personnel costs
Environmentally friendly operation by hood and exhaust, and combustion chamber
Rotating switch
MAERZ TBRC is a specialized instrument for the production of brass and precious metals. A central feature of the Top Turning Transformer (TBRC) is its high melting and refining efficiency. Typical input materials include different quality copper alloys, alloys containing precious metals from lead production, and anode lubricants from copper electrolysis. Depending on the task, various water-cooled types are used to melt, oxidize and reduce.
High performance is achieved through variable rotation speed of the vessel combined with the use of oxygen technology. By rotating in the melting process, the hot lining continuously underneath the material is cooled, resulting in optimum heating performance. In addition, the refining process is accelerated by continuous mixing of liquid baths. For castings or reductions, the entire conversion vessel can be tilted to cast into a washing machine or truck. Capacity ranges from 5 to 50 tons and even more can be achieved using different designs.
Advantages of TBRC
Fast and efficient melting and refining
Reduce metallurgical processing time
Suitable for refined copper and precious metals
Unique unit for melting, refining and casting
Rapid exchange of ship furnace for relining
MAERZ® rotary fireplaces
In the rotary kiln, the material is heated to a temperature between 500 and approximately. 1,350 ° C. Typical furnace capacity is approx. 20-120 t / h. For heating a rotary heater, regenerative burners are also applied next to the heater.
Turning table MAERZ® furnace
In the rotary kiln, the material is heated to a temperature between 500 and approximately. 1,350 ° C. Typical furnace capacity is approx. 2-20 t / h. In addition to burners, regenerative burners are also used to heat the kiln.
MAERZ® pusher-type furnace
In the oven type, the material is heated to a temperature between about 1200 and 1.300 ° C. Typical kiln output is approximately. 50-250 t / h. For heating pusher furnace, regenerative burners are also applied next to the burners.
MAERZ® fireplace walk / kiln walk
In the walking / fireplace heater, the material is heated to temperatures up to 1,300 ° C. Typical kiln output is approx. 30-350 t / h. For heating of the walking / walking heater fireplace, regenerative burners are also applied next to the burners.
MAERZ® pusher-type furnace
Plate materials are heated in large-scale pusher furnaces with temperature
up to 1.32 0 ° C. Typical oven performance is 100-300 t / h. Heating is a combination of burner, roof and regenerator
MAERZ® walking jumbo burner
Plate material is heated in a large-scale chiller to a temperature of up to 1,300 ° C. Typical kiln efficiency is 100-450 t / h.
Heating is a combination of burners, roofs and burners
MAERZ® Technology
Andritz Maerz flat-burning fireplaces are designed to look at aspects
energy optimization and reduced emissions. This burner can work with all types of fuel and air preliminarily. The GPL: NOX values associated with 5% O2 in the exhaust gas are below <200 mg / Nm3 (at an air heating temperature of 500 ° C and a chamber temperature oven 1,270 ° C).
MAERZ® bed bottom burner
Designed as a heat treatment furnace for a temperature range of 100 up to 1150 ° C,
For heat treatment in forging plants, foundries, heat treatment plants only
the steel industry as well as in the non-ferrous metal industry. Maximum fee: 500 tons.
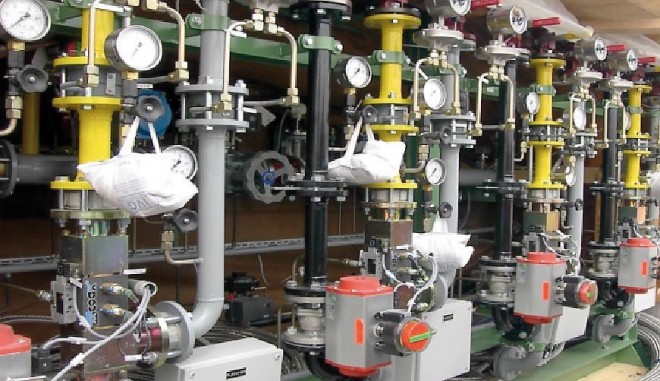
MAERZ® furnace hood style
This type of furnace is used for the whole process of forging through heat treatment
, for special applications. Working temperature ranges from 200 to approx.
1,150 ° C. The cover or lid is moved automatically, by traveling
Crane or other suitable lifting device.
Heat treatment MAERZ® burner
These plants are used for the whole process of "forging through heat treatment
, for special applications. Temperature ranges from 700 to approx. 1,150 ° C
The cover is moved automatically by means of a moving crane or other sufficiently lifting device.
ANDRITZ Maerz supplies
Rotary kiln systems for copper and precious metal alloys.
The product range includes melting and refining furnaces for primary and secondary
Copper production, as well as for the copper material processing industry
such as cathode and high quality iron scrap. Moreover, we supply adapter for copper and precious metals refining.
Process optimization technology allows the production of high quality products
Produces strings, tubes and formats, as well as producing anode for electrolysis.
optimum oven geometry. The material is loaded into the shaft with a skip. The burners are completely installed around the lower shaft and supply the molten energy. Gas emissions move upward through the solid waste pre-heating shaft at the top of the shaft. Copper fluid can be supplied by means of a pot or washing machine to the following process step.
Incandescent furnaces are also equipped with fireplaces that allow for refuge and can continue liquid copper treatment. Due to that fact, also low quality scrap can be used. The molten copper is passed through, refining the furnace. Production capacity up to 90 t / h can be made.
In order to have effective different quality copper melting, ANDRITZ Maerz supplies shaft furnace and fireplace. MAERZ® furnaces allow the melting of copper cathodes, anode residues and high-grade copper scrap with very high energy efficiency. High efficiency is achieved with the MAERZ® recorder system with one controller and one recorder
Advantages:
Fast and continuous melting
Optimize thermal performance
Preheating of waste prior to upstream influx of off-line gas
Apply for different qualities scrap
The MAERZ ® TBRC (Top Blowing Converter) is a general purpose unit
for copper and precious metals production. A central feature of TBRC is a highly efficient melting and refining process.
Typical input materials are copper scrap of different qualities, precious metals
Alloys of lead and anode mud from copper electrolysis. Depending on the task, various water-cooled lances are used for melting, oxidation and reduction.
Responsible for the high efficiency that is besides the use of rotary-speed rotary-speed rotary technology. Due to the rotation during the melting process, the hot lining continuously rotates beneath the cold material, resulting in an efficient heating system. In addition, the refining process is accelerated by continuous mixing of the liquid bath. To cast or remove, the entire conversion vessel can be cast to the washer or truck.
Capacity of 5 to 50 tons and even more can be made using different designs
Advantages:
Fast and efficient melting and refining
Less treatment times
Suitable for refined copper and precious metals
Unique unit for melting, refining and casting
Rapid exchange of ship furnace for relining
Technical packages and equipment to modernize and optimize existing plants. These packages are intended to increase metal yield and metallurgical efficiency and optimize energy use by improving Process Technology. Refined packets contain other:
- Fine-tune system
- Combustion system with or without oxygen
- Nitrogen cleaning system
- FEM calculation
- CFD calculation
Advantages:
- higher than copper output
- High-grade copper production
- Shorten processing time due to higher process efficiency
- The bath movement is stronger due to the stirring of special elements arranged in the furnace
- Optimized cancellation procedures due to special arrangements
- Better heat utilization due to optimized heat transfer