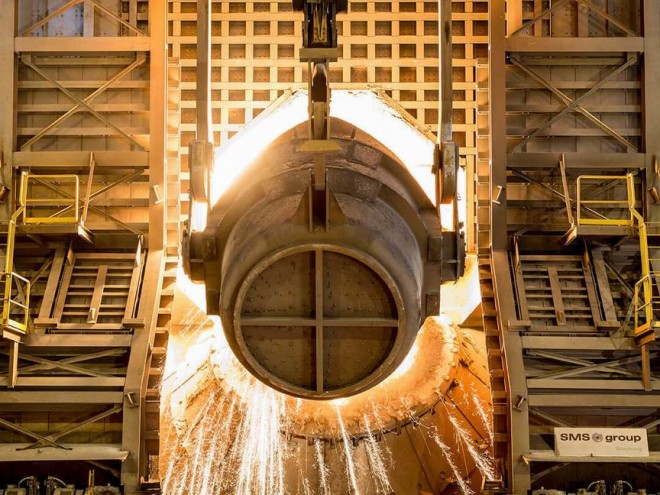
PLANNING OXYGEN WITH STEEL IN THE FUTURE
We have accumulated a wealth of experience from countless projects that we can precisely adjust our solutions to your process and specifications. You also benefit from our experienced managers, engineers and technicians. They are all very familiar with different environments that you can count on for a minimal interruption. Simply put, most of your current production processes continue to run uninterrupted.
THE FOLLOWING HERE IS THE FOLLOWING FOLLOWING:
Strictly follow your time plan
The simulation process reflects the plant layout and your requirements
Integrated automation packages
Habits have tried and tested
Producing stainless steel in the future
Low production cost, high productivity
The special thing about our production process is that we will adjust the factory to suit your conditions. Included in these considerations is the availability of materials, infrastructure, and power supply.
As a result you can produce high quality materials at low cost.
MANUFACTURE OF STAINLESS STEEL UNDER FUTURE ORIENTATIONS
LOWER PRODUCTION COST, HIGH CAPACITY
Low inert gas consumption
Reduced material consumption
Processing time is short
FLEXIBLE
Scrap distillation
Unlimited C and S-content of raw material
Most of the steel can be processed
OXY HIGH QUALITY COMFORT WITH TEMPERATURE
HIGH CROM
We distinguish between Duplex (single phase degasser) and Triplex (two stage decarbonisation).
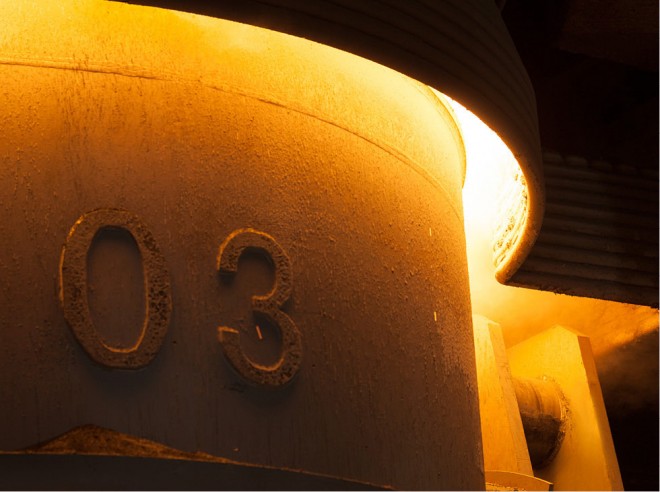
An efficient vacuum converter, according to custom design
Combined with AOD and VOD technology
We specially develop vacuum transformers for the production of stainless steels, acid and heat resistant steels as well as special alloy steels, manganese, and chromium alloys, together with ferromanganese and secondary ferrochrome carbon. average and low.
REFRIGERATED STEEL AND FERRO SYNTHETIC
Our technology helps you achieve ultra-low carbon, nitrogen and hydrogen components. Used as a reactive gas, CO2 gas has a powerful cooling effect during vacuum degassing. This means you save metal coolers when handling ferrochrome and ferromanganese. You also consume less argon. The entire technical process ensures the lowest operating costs.
THIS IS YOUR BENEFITS FROM THE TWO SALT STAGES THROUGH OUR STABILIZER IN OUR CHILDREN:
AOD process at ambient pressure for medium carbon layers
Desalination and de-gasification under vacuum for steel and ferro alloys with low and extremely low carbon and nitrogen content.
AOD vacuum and vacuum operated vacuum feet are mounted on a sleigh. That makes it easy to move them between the two treatment steps.
Modernize to increase your usage rate
All the replacements and improvements in your converted steel plant pursue this centered goal: the ability to produce more steel than the same time in your existing plant. Achieving this goal means that your steel mill can provide the market with higher productivity - at a lower cost.
This creates a clear competitive advantage for you, especially in times of high demand. However, even if demand is stagnant or down, the cost benefit per ton will give you more flexibility and therefore more security that you can always deliver the right segment of the market.
BOF TRANSFORMER TECHNOLOGY - DYNAMIC
Your benefits from the workshop in Hilchenbach:
Modern workshop in Hilchenbach / Germany
Large number of strong machines
Power tools
Welding shop and assembly equipment in front of embryos up to 450 t
Blank only from selected sub-suppliers
Strict requirements: degree of deformation, material cleanliness → mechanical properties are guaranteed
One of the few manufacturers in the world capable of producing reinforced or heat-treated gears with a diameter of 6,000 mm
Complete mechanical arc welding with welding seams 100%
The gears in numerical rolling machines
Disassembled SMS group assemblies are ready to be assembled with the modified dental contact model
More than 60 references on the tilt of the adapter since 2002
Pan no maintenance
Heat expands in all directions
Easily upgrade existing conversion equipment
Design has been improved continuously for over 47 years
Maximum metallurgical volume due to small design
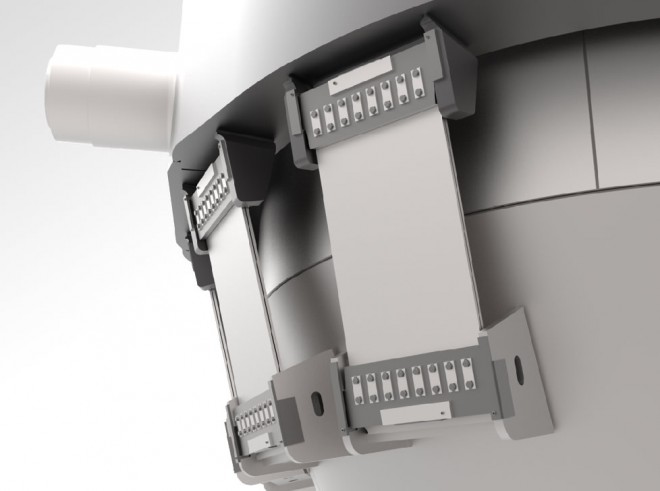