Factories, production, biogas, - Finland
Supply, equipment, technology, general contractor EPC - Finland
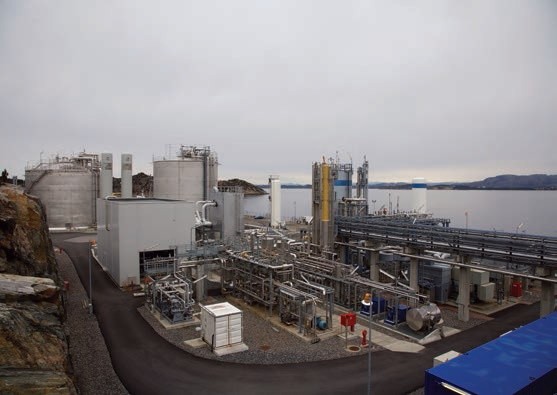
Our solution
Wärtsilä provides innovative, reliable and cost-effective solutions in the design and engineering of LNG production plants that are suitable for small to medium sized liquid applications.
We have provided a number of complete shore-based LNG facilities, including the introduction of an improved liquefied system with two extension machines based on the Brayton reverse cycle. The LNG for Gasum plant in Finland uses excess nitrogen (LNG) for LNG production and incorporates a new technology that reduces LIN consumption by up to 50%.
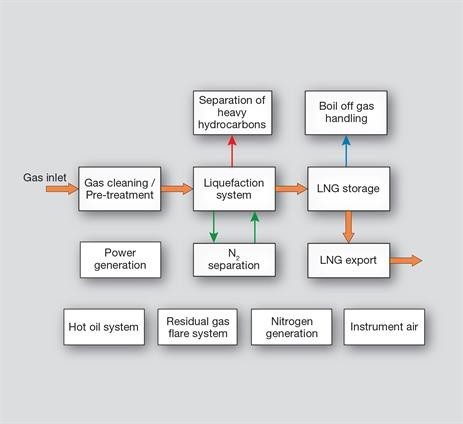
The EGE Biogass plant in Oslo, Norway, can convert household food into liquid waste, which can produce enough fuel to run 135 buses.
Our LNG facility in Snurrevarden, Norway, is fully equipped with remote monitoring and control capabilities, being the first small scale LNG plant in Northern Europe.
LIQUID PROCESSES - Modular Solutions
Many different types of gas, both in quality and quantity, require a variety of liquefaction systems.
Wärtsilä's solution for this is a module based on the design, where each module is optimized for the process for which it was intended.
The diagram (below) shows the different types of modules that can be supplied in a liquefied plant provided by Wärtsilä.
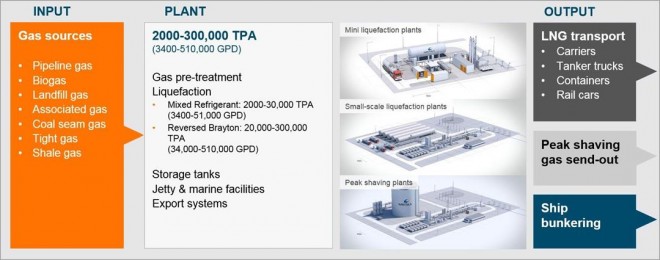
Reduced environmental requirements for emissions
- Fuel for ships. By the end of 2015, about 90 will be fueled by LNG. It is cost competitive and contributes to reducing greenhouse gas emissions.
- Fuel for heavy truck transport. Currently there are about 170,000 trucks and buses operating on LNG in Asia, 3,500 in North America and 1,500 Europe.
- Rapid growth of renewable energy sources in mixed power generation increases the demand for gas power plants for load balancing.
- Liquefied petroleum gas (LBG) is a locally produced, CO2-neutral biofuel
Availability of subsidies in the EU and China for
LNG infrastructure projects
• Energy needs
- Need for lower energy costs in power generation and power.
- Energy security considerations.
- Demand for power distribution in some areas.
Small- and medium-scale liquefied natural gas plants are increasingly attractive to large-scale LNG infrastructure. Technological advances have made little money from gas reserves and can be stuck in new locations. This opens the door for business owners and energy companies to take advantage of the growing LNG market.
Wärtsilä technology has been developed specifically to overcome the typical small-scale challenges of the LNG project using principles such as modularization, standardization, simplicity, flexibility, and operation. maintain lean strategy. This allows very competitive capital and operating costs for LNG plants with a capacity of up to 300,000 TPA.
BIOGAS LIQUEFACTION
Biogas is a renewable energy source, and therefore biogas liquids (LBG) can be described as a renewable fuel. However, the amount of biogas at any location is far lower than that of natural gas reservoirs. Wärtsilä has developed a comprehensive solution for cleaning and liquefying biogas. It has been developed specifically to overcome the technological and economic challenges of small liquefaction.
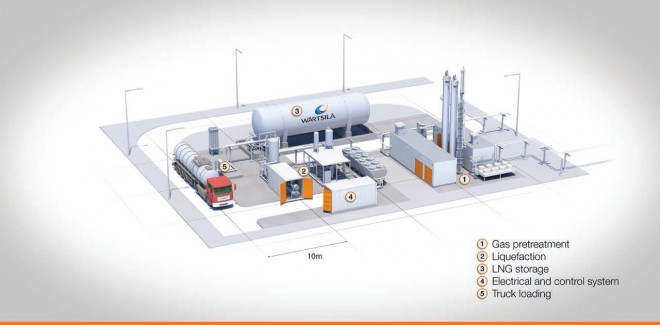
BENEFIT
• LBG always contains 99% CH4 - a premium product with very high methane content.
• LBG and conventional LNG can be used in the same way using the same infrastructure.
• The production and use of LBG contribute positively to the environment. Wärtsilä has many years of experience in the development of liquid technology for small scale applications. We understand the importance of operational simplicity, flexibility, efficiency, robust equipment and compact footprint when dealing with small scale LNG projects. The bottom line is that there must be a profitable project for the owner. These possibilities are well expressed in our references.
The Wärtsilä liquefaction technologies are based on two processes; Composite Cooling (MR) (mixed) and Revented Brayton process. Both are designed with closed loop cycles, thus eliminating makeup or chemical / logistical treatment for refrigerants. The main elements of the plant are listed below, while different modules can be combined to improve the efficiency of the plant as required by the specific project.
MAIN SYSTEM
• Gas / feed
• Gas treatment
• Liquid
• LNG storage
• Export of LNG
OTHER SYSTEMS
• Power production
• Compressed air
• Hot oil system
• Separation of heavy hydrocarbons
• Handling of combustible gases
PRESENTATION (MIXT PRESENTATION)
Wärtsilä's MR process is based on a simple screw compressor and exclusive chiller mix. Thanks to a buffer system, it is a complete closed loop solution without having to refill after starting and stopping procedures. It is based on the standard components to provide low investment cost and rapid production of the module. With a suitable refrigerant mix, an intelligent automation system and standard components, Wärtsilä was able to combine the high efficiency of the MR process, with the simplicity needed in smaller plants. Wärtsilä's MR solution is perfect for biogas and liquefied natural gas plants below 50 TPD (ton / day). For this liquefaction, we provide standard capacity of 10, 17 and 25 TPD.
Ability to produce -2,000 to 30,000 TPA
Cooling system - Exclusive hydrocarbon mixture in a closed loop
Energy consumption - Only 0.70 kWh / kg, depending on the specific conditions of the project
Technology Features - Off-the-shelf components allow for cheaper, quicker distribution and simpler maintenance.
Installation - Plug-and-play design with standard size 10, 17 and 25 TPD is delivered within 12 months
MAKE A BREATH
In this process, nitrogen is the only refrigerant and is produced directly from the air. Nitrogen is compressed and expanded to reach the required concentration. Brayton's patented Wärtsilä parallel cycle improves further and refines the reverse. Brayton process for low power consumption. These liquefied plants are easy to operate, reliable, fully automatic and cost-effective for the low life cycle of small liquids.
For liquefied plants requiring more than 15,000 cubic meters of storage, the bottom flask will become an option. The final choice depends on cost, delivery schedule and delivery requirements. Typical considerations that need to be taken include the distance to consumer LNG, consumption rates, additional schedules and whether the LNG plant is operating on weekends or holidays. This information provides an index of the minimum number of buffer days for LNG storage. The establishment of an export system is configured based on which transport infrastructure best serves the desired customer. LNG carriers are often the best choice for coastal facilities when relatively large volumes of LNG are shipped. Oil tankers are often used to distribute LNG from local liquefied plants. Some liquefaction plants also offer the ability to bunkering vessels or filling up LNG-fueled trucks.
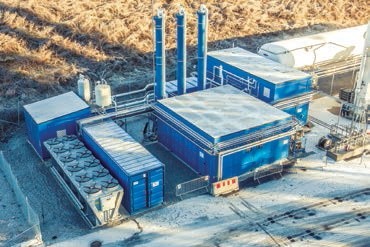
Capacity - Single tank 100-1200 m3
Many tanks are 100 - 20,000 m3
Boiling gas (holding mode) - 0.05 - 0.15% / day, but the tank is capable of processing
Pressure increased to 1 month
Operating pressure - 0.5 - 4.0 barg
Production method - Made in the factory
Installation time on site - Days to weeks
The projects are tailored to the needs of the client based on a set of predefined ranges and proven design to provide a high quality property at competitive prices. The range and quality of our service puts Wärtsilä apart from its competitors, and our range of capabilities is unique. We provide:
• Advice and assistance in arranging structures and finance, including financial models and feasibility studies, if required.
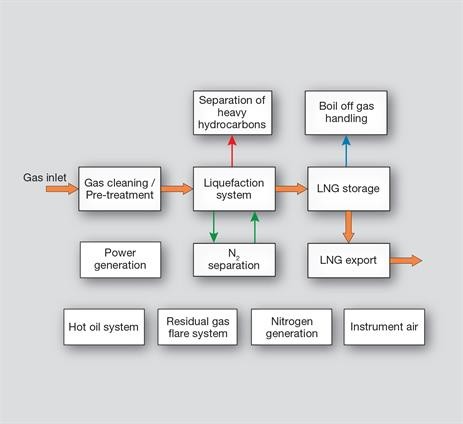
Proven LNG infrastructure solutions have been designed by the LNG team world-class.
• Provide full technical, procurement and construction (EPC) services at guaranteed prices, schedules and performance, as well as providing processing solutions.
• Use professional project management methods and best practices.
Operation & maintenance contracts for performance are guaranteed and maintenance costs can be expected.
• The combination of liquefied petroleum gas (EPC) and power plants generates significant resonance benefits. Wärtsilä is proud to serve every customer with the same quality and excellence to ensure that all expectations and priorities are understood and fulfilled.