Thiết bị và công nghệ sản xuất,bao bì, nhựa PET-Italy
Equipment and technology of production, packaging, plastic PET-Italy
BOX WITH PLASTIC
Since the original circulation of PVC resins and PET containers, the company began to develop systems and lines for their processing and handling. ZECCHETTI has produced Italy's leading palletizer for PET bottle processing. The success of the "most modern" machine has pushed Zecchetti to continually expand its production range to include all types of equipment and accessories needed to meet the rapidly growing demand for the speed and flexibility and the supply chain complete by providing the same reliability and efficiency standards. The long-standing experience in handling plastic and PET containers has enabled Zecchetti's designers and engineers to be able to manage all technical problems that may arise due to the material being used.
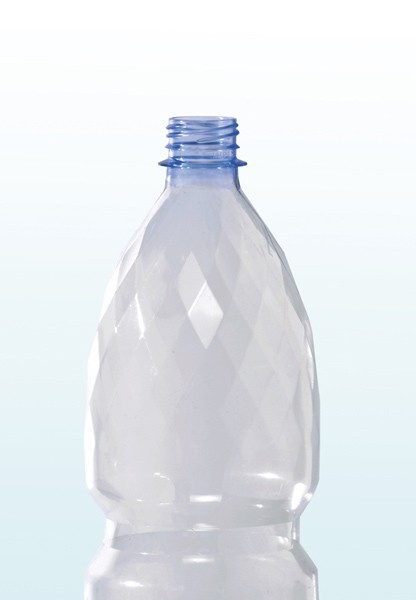
EXPERIENCE EXPERIENCE & REVELATION
Ten years after the first PVC container shipment (in the early 1980s), followed by PET containers, Zecchetti was recognized (and still is) the first manufacturer / handling empty PET bottles in the world. All plastic bottles (PET, PVC, HDPE) regardless of their shape, can be Zecchetti Equipment, even smaller and lighter boxes, and of course includes 5 liters. tank; All plastic bottles for the most diverse sectors (beverage, water, wine, chemical products, ...). The technology developed by Zecchetti certainly solves any problems that may arise from the unstable, sticky, electric charge. The history and experience of empty container handling makes Zecchetti debug all devices to the point where they can ensure smooth operation and maximum efficiency. This means that now the commitment is to make life easier for our customers and help them reduce production costs. Based on the above guidelines, we will introduce the following general concepts related to all of our products.
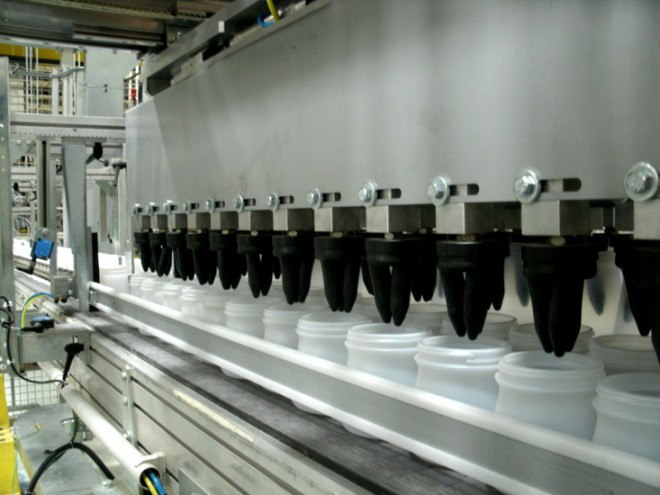
Zecchetti was one of the first manufacturers to introduce an automatic format change (eg side-by-side instructions). Today, we can boast of very complex line management that allows for functional and flexible adjustments in all areas. In fact, intelligent control systems are provided with self-diagnostic capabilities and can be performed individually or in groups.
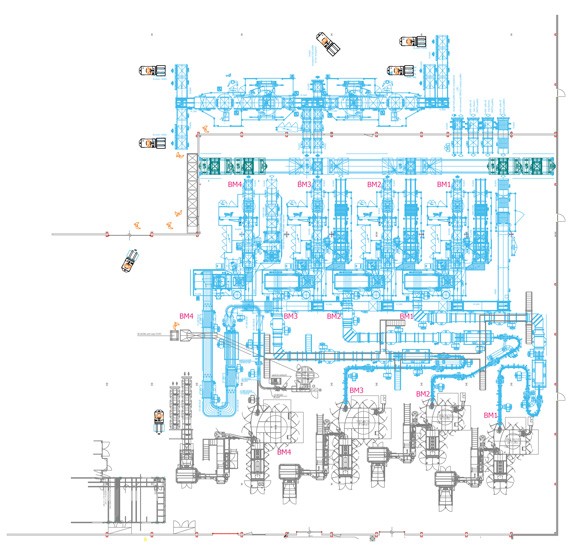
Very often the transmission line extends many meters or even at different levels of the same plant. For this reason, we think will provide a tool that allows action on the transfer line from wherever the operator is located. Walking pad allows for the adjustment of each single control group of the line and saves this change in the formula without having to operate on the main board (for example: Motor speed, driving position, etc.). The walk table presents all the main functions of the remote control panel such as, line function settings, line status information and alarms, etc. This means the line also has Can be monitored remotely.
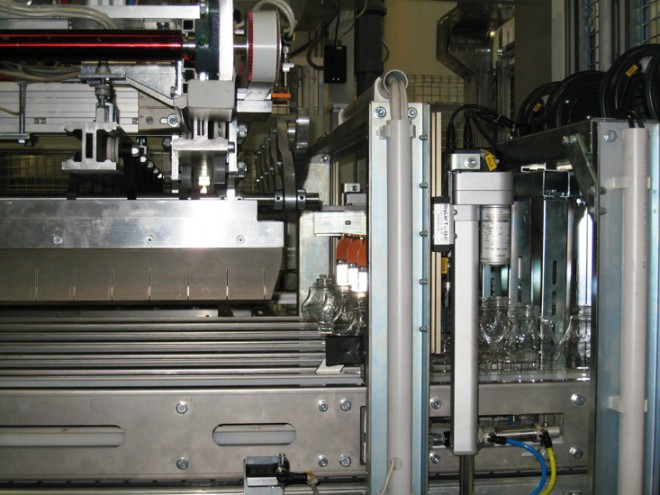
The operational philosophy developed by Zecchetti is designed to intelligently adjust the engine speed, based on the different conditions of the flow to minimize the power requirements and installation capacity of the line. The activation of such a system requires a PLC control, variable frequency drives and a touch panel.
Zecchetti proposes a highly developed, user-friendly monitoring software with great flexibility in setting up formulas to ensure maximum performance and minimum change time.
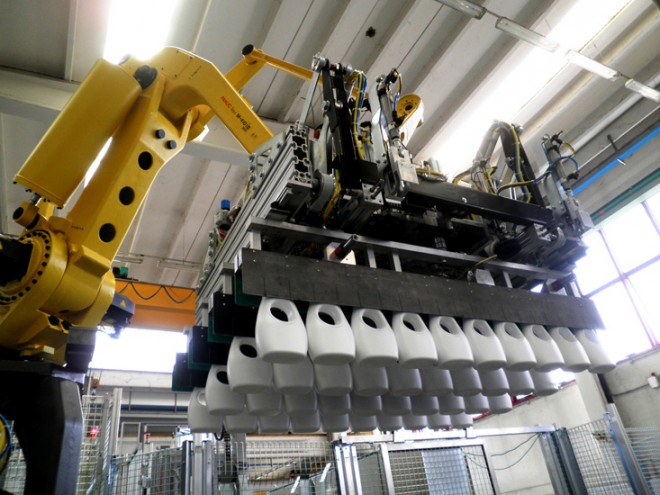
FUNCTIONALITY
The overall performance of the whole line, even on remote monitoring PCs or mobile devices. Simple and instant access to any part of the line by selecting it.
Ability to modify line parameters.
Show each motor speed.
Display of each single absorption motor.
Adjust the speed of the engine.
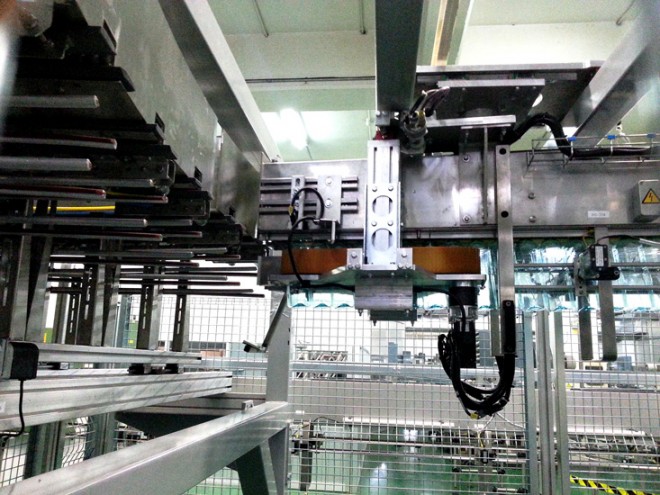
PROTECT D DATA MATERIALS
6 security levels and configurations can be accessed with a password.
DIRECTION D RECN
Can create a new formula by typing the new bottle diameter.
Ability to save / load / delete recipes.
Ability to set up offline for any formula while the machine is running.
MANUFACTURING DATA
Up to 4 shifts can be set.
Shows the production history of any stage.
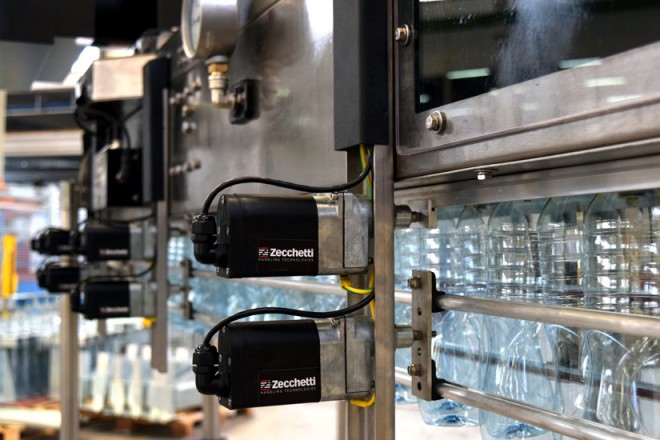
Alarm management
Display active alarms with appropriate help.
Displays alarm history for a certain time period.
Display alarm statistics for a certain time period.
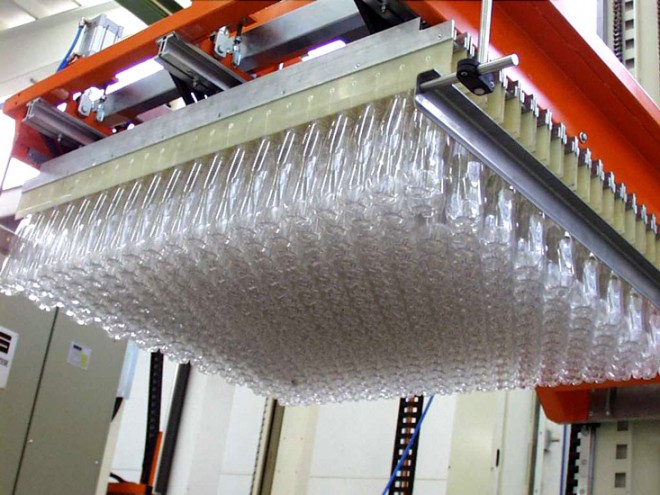
AIR MOVE THE FASTEST AND MOST SECURE WAY TO BOTTLE PET BOTTLE EMPTY
TRUST experts
Zecchetti's long history and experience in the field of container shipping enable deep understanding of the technical requirements of a wide range of air conveying applications. Other conveyor applications are very simple and some are difficult. The ability to see the difference, before the system is installed and running, and the ability to use proven technical concepts to take away the "black art" of conveyor system design only comes from from experience. The most successful conveyor system is made up of proven hardware coupled with an integrated automation system and a layout design that fits into the application or application with a degree of flexibility. Zecchetti was one of the first Italian manufacturers, if not the first to produce air conveyors. For nearly 25 years,
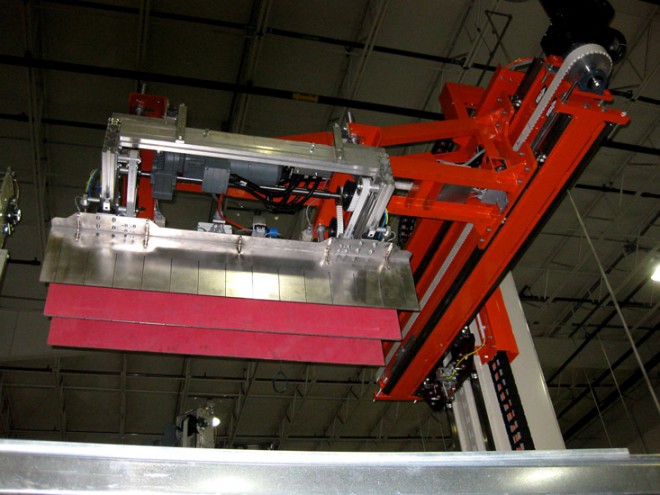
EFFICIENCY AND ENERGY DESIGN TO IMPLEMENT
Energy efficiency and energy savings are the key words of the Zecchetti R & D Department. Air transport designs have been designed to increase the air pressure within the OMEGA frame. The trays are oriented precisely (through which the air is blown) and the perfect frame of the frame allows the removal of air loss and therefore increases the air pressure inside.
Consequently, the number of fans needed to be automatically reduced to Energy Saving.
Speed control
Continuous transport speed control. A feed from the downstream stream allows keeping a constant speed, eliminating any issues arising from ambient / climatic conditions and keeping the filtered effect under control.
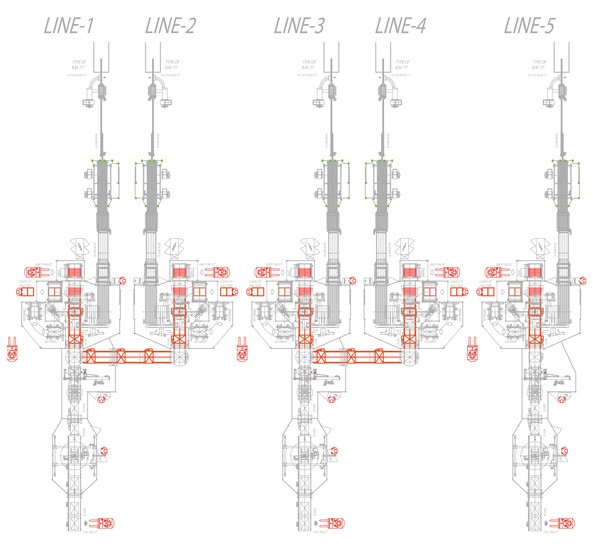
MODERN FOR FLEECE TOP
Due to its long experience in the handling of empty plastic containers, ZECCHETTI can propose safe technical solutions for even very light and unstable bottles that can not be shipped "by air". Extremely detailed care, along with continuous improvement research, enables the delivery of high performance, high-speed transport systems.
The main objective of the TABLE TOP transport system is to ensure smooth, efficient and safe transport of containers. To be successful in this, every detail is made of high quality materials and each critical area is designed with the right solution.
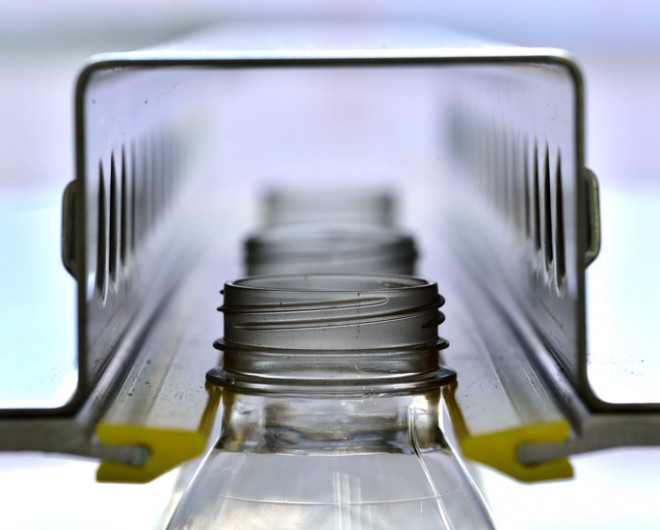
ROTARY COLUMN ANALYSIS TOP PAGE
Modular pallet stackers. "R-PAL", moving the bottle layers, is the highest expression of important features such as flexibility and accessibility. Its modular design allows it to fit any type of layout, bottle type and production. In fact, it can start with a modest investment and upgrade the route in the future. The three-axis operation design, which was born 30 years ago and was made with the Zecchetti rotary column, has been developed over the years to increase reliability, flexibility and performance. Its success has been enhanced by more than 1000 units operating worldwide. Zecchetti's Palletizer "R-PAL", thanks to its modularity, represents the ideal solution for short, medium and long term investments.
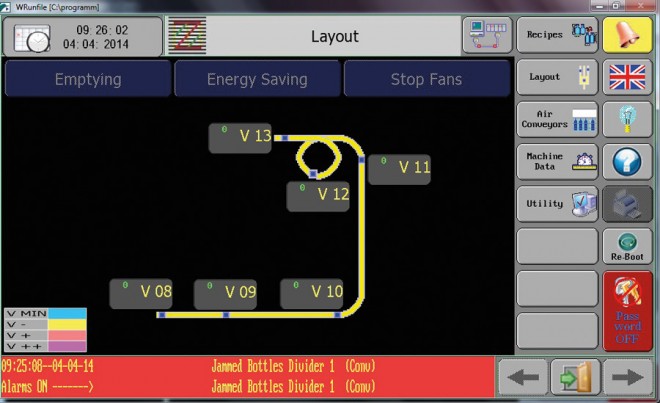
SOLUTION
The Row By Easy Pal solution offers container handling and automation technology for optimum performance in today's high-volume production environments. It represents the solution that has the best ratio between performance and floor area of the dress.
Bottles are taken from the feeding system, compressed and placed directly on the pallet. Continuous bottle control and the absence of panel formations contribute to safely handling unstable and lighter bottles.
This generation of machines makes life "as easy" as possible, requiring very little operator intervention. Sensitive, TTC-AIR, meaning that all bottle shapes can be processed.
SOLUTION FOR ALL PLASTIC CONTAINER NEEDS
HANDLING 60 years of experience in automated machinery production allows Zecchetti to introduce a range of equipment that can meet all of the hollow plastic processing needs. Furthermore, thanks to the "Zmagazzini" Shipping Division, Zecchetti can also propose automated solutions for full pallet storage and loading them into trucks. High benefits are also the vertical automated warehouses used for "orderly" storage, in space optimization and in the way of protection of spare parts, changing parts and molds.
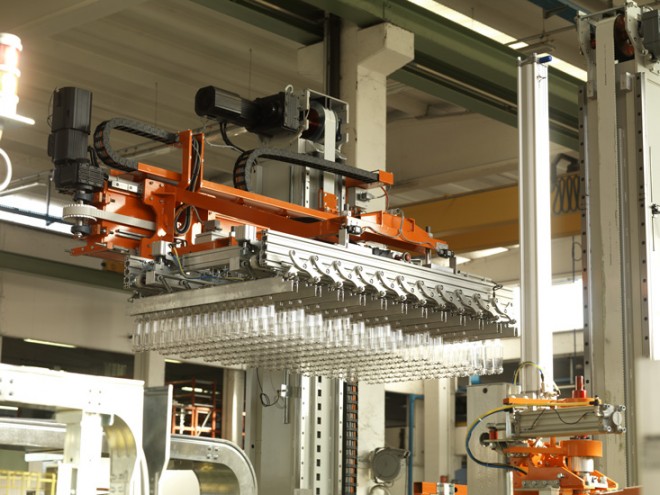
In order to complete the automatic lines, a number of modules for pallet movement are required. It is essential that these conveyors are designed to fit all existing pallets. In fact, it is important that these conveyors go to the changing station in a smooth and smooth manner. Only in this way will the load be protected by preventing the collapse of the container, especially the external parts, from damaging the entire pallet at the expense of product quality. It is extremely important that their design allows them to be surpassed by operators, if necessary, and make them protected against "FLT" attacks. Many solutions are available to meet every need.