Aluminum Casting Plant - Equipment & Technology Germany
LEADING TECHNOLOGY IN ALUMINUM FACTORY
Design, supply, build and pay for the aluminum SMS group worldwide. It focuses specifically on aluminum warehouses, providing:
1. Horizontal casting plant for bars, rods and billets
2. Molding factory for extrusion and forging
3. Open molded parts (air and chilled water)
Casting horizontal, vertical, or molded castings?
All these methods have their value, and are suitable for different applications.

HORIZONTAL, PURPOSE, OR MOLDING?
All these methods have their value, and are suitable for different applications.
If you want to produce embossed main castings, vertical casting is your first choice. You achieve smooth workpiece surface with air slider molding technology. That is because it minimizes deposits in the extruder. This also applies to rolled sheets. Here, casting in a magnetic field significantly reduces the skin area. However, compared to the HDC process, the VDC process comes with some basic limitations.
The wheels of VDC are more expensive. Why? Because they need higher ceilings, overhead cranes, and foundation for foundry.
The semi-continuous nature of VDC results in reduced productivity.
The procedure involves the establishment of many labor-intensive jobs for each failure. In contrast, HDC usually achieves continuous production running from 3 to 20 days.
Just one or two operators per shift to create a T bar (two operators for starting and stopping actors).
VDC does not have built-in saws. They require an additional saw plus operator. The HDC molding is well done because the cutting machine automatically cuts the T-bar to last without interrupting the molding process.
Finally, the VDC process does not produce products with small areas that are cost effective or have quality requirements.
Metal insertion into molds opens waste:
Traditionally, sows, pigs, and ingots are produced using molds. Although the technology has improved over the years, the formation and deposition of the fringes are inevitable. Cascading causes chaos in the molding process. This shows a relatively large surface area to the atmosphere for oxidation. The main thing that affects the formation of ice is the metal temperature, the pouring height, and the pour rate.

Our HDC plant almost eliminates waste. You save money by avoiding the loss and metal breakage. Here is how the process works:
First, the metal flows smoothly through the dishwasher and tundish, protected by an undisturbed oxide layer. There is no opportunity for oxides and other impurities to enter the product.
Subsequently, HDC molded bars and casts were chilled at least ten times faster than sows and pigs. This ensures smooth and even uniform structure as well as uniform analysis throughout the molding product.
Another way to improve the quality of the remelt product is to combine the HDC process with an in-line degasser and foam filter (CFF). Working together, these systems produce T-bars and castings without porosity and adhesion.
These are the advantages of the HDC alloy casts compared to castings in the die castings:
Low hydrogen and extremely low oxide oxides
Smooth, uniform structure
Unification, unification of content and distribution of alloy elements. No gravitational separation
No cracks, shrinkage, or water stains. Size, straightness and weight
Smooth surface makes stacking and bundles compact
All this means that: continuous horizontal workers really deserve the "universal weapon"

This flexible device is ideal for production:
Iron bar and anode bar
Cast steel
You can produce all products on the same machine. Each one has a dedicated exit on the downstream of the flywheel.
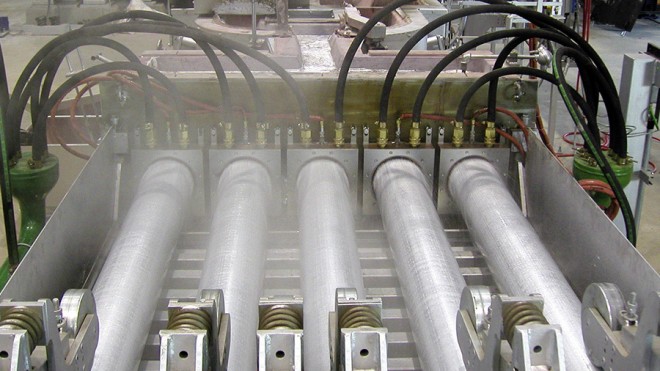
VEHICLES
This flexible device is ideal for the production of Foundry billets, busbars and anodes, T bars and extruded bars. You can produce all products on the same machine. Each one has a dedicated exit on the downstream of the flywheel. Providing all exits system is installed, your operator can change in one shift. All they need to do is get a different set of molds and load the new cast formula for the computer. Continuous continuous process, the HDC process has allowed itself automation. That's because all downstream equipment is perfectly suited to casting machines and does not require additional staff. Sawing, weighing, stamping, marking, labeling, stacking and strapping: these are processes that run automatically. Now, following continuous improvements over the years, our factory features automatic start and stop castings as well as automatic tuning of the chiller system. Precise control comes from the Hertwich PLC-PLC system, which includes error-correction and menu error management formulas. Moreover, all important parameters of the plant are monitored, controlled, and stored for the computer for subsequent processing.

MEASURING KIM
Melt without any disturbance from the furnace to the casting body. Then, it passes through the transition tubes into the mold that is completely shielded from the atmosphere. This means that no oxide can form and enter the embryo. A three meter builder can cast 30 strands at a time - each with a cross section of 75 x 54 mm. Depending on the alloy, casting rates range from 400 to 600 mm / min.

MEASURING KIM
Melt without any disturbance from the furnace to the casting body. Then, it passes through the transition tubes into the mold that is completely shielded from the atmosphere. This means that no oxide can form and enter the embryo. A three meter wide machine can cast 30 strands at a time - each with a 75 x 54 mm cross-section. Depending on the alloy, casting rates range from 400 to 600 mm / min. Next, the saw cuts the fibers into ingots 650 to 750 mm long.
The ingots are marked with alloys and castings, then stacked. Finally, the finished bundles are packed and, if necessary, wrapped in stretch foil and marked colors. When the bundles arrive at the weighing table, they receive heavy tickets, then transfer to the storage conveyor, which can accumulate as much as 32 bundles. All these steps are done automatically.
The plant handles a wide range of alloys, from pure aluminum to 12% silicon and up to 5% magnesium. The most popular HDC tower comes with a width of 3,000 mm. It is capable of up to 13 tons / hour of T-bars or 8 tph of castings. The largest HDC processing machine that HE has ever manufactured is designed to cast 4 bands of 850 x 300 mm or 24 strips of 106 x 106 mm simultaneously. Continuous production achieved 17 tph for T-bars and 12 tph for ingots

TARA
Currently, these plants produce T-bars (850 x 300 mm) containing up to 11% silicon with a maximum capacity of 17 tph. The T-bar from our HDC meets the highest requirements of our customers. They have a homogeneous seed structure. In addition, each piece and batch have a consistent chemical composition. Equally important to your customers, the T-bar has no impurities, voids and cracks
Currently, these plants produce T-bars (850 x 300 mm) containing up to 11% silicon with a maximum capacity of 17 tph. The T-bar from our HDC meets the highest requirements of our customers. They have a homogeneous seed structure. In addition, each piece and batch have a consistent chemical composition. Equally important to your customers, the T-bar has no impurities, voids and cracks.

THANH AND DRINKING
Normally, the original aluminum manufacturers first bought an HDC factory to produce busbars for building the budline. Especially here the plants are also designed for later conversion to molded products.
What makes these barriers stand out is their excellent electrical conductivity, perfect surface finish and excellent straightness. In addition, HDC conduit production is much cheaper than VDC
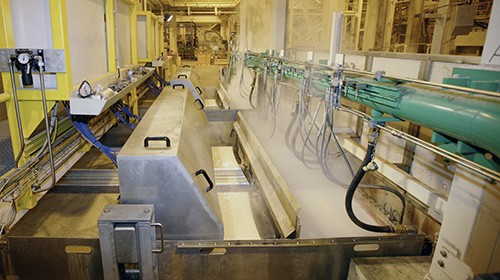
THANH AND DRINKING
Normally, the original aluminum manufacturers first bought an HDC factory to produce busbars for building the budline. Especially here the plants are also designed for later conversion to molded products.
What makes these barriers stand out is their excellent electrical conductivity, perfect surface finish and excellent straightness. In addition, HDC conduit production is much cheaper than VDC. Airplanes directly cut down the transmission rods continuously to accurately complete the length from 0.6 m to 20 m. Even better: no need for additional cutting, so you will benefit from less weld.
These plants are ideal if you operate your own mill for recycling of extruded or forged scrap. Available here is the capacity of up to 50,000 tons per year in diameter range from 80 to 380 mm.

MAKE MOLD CASTINGS
Not only did you get castings using Hertwich's cooling water. We also offer you an air-cooled version. It comes with some enhancements and offers an attractive alternative to water-cooled solutions. Common for both types is excellent performance, reliability, and product quality.
The dishwasher is used by Hertwich instead of the cast wheel to reduce the floor effect. That significantly reduces the formation of ice. It also ensures homogeneous heights. You choose the last packing station you want, including stacking, strapping, scales, or marking equipment. All of these are available in automatic or manual versions. Simply enter your recipe, and start casting automatically ensures perfect safety and user-friendliness.
HOT WATER COOLING MACHINE
In hot, water-cooled countries it is essential to achieve the desired production rate. Precast molded parts are often water-cooled as a cheap and simple way to solidify liquid metal.
HEAT-FREE AIR COOLING BOILERS
You can also freeze and cool your own ingots with air.
Here are your benefits compared to water-cooled:
Better quality embryos
No narrowing holes or cavities, no heating is not dangerous
No hydrogen pick-up
Less wear, prolongs the life of the mold
Less maintenance
No pit
No water infrastructure
Cooling of the molds, secondary cooling of the bars in the chaotic cooling tower
.