Aluminum Bars Factory - USA
Supplying equipment and transferring production technology
Z1 RA / Embossing machine
Equipment is designed to store the pieces and feed them to the fireplace heater.
The sturdy structure is made of welded steel which is controlled by a round log conveyor.
Hydraulic system with cylinder and flow compensation to ensure accurately loading logs and avoiding shocks.
Precise movements are made at very low noise levels and the log is placed exactly on the shaft.
Soft guide on the push wood.
The power supply is driven from a gear unit, located near the entrance of the furnace, equipped with a feedback position to control the input length of the registers.
Quickly replace the alloy due to the 0º slope
Z1 CB / cuttings
The device is designed to comb the logs before entering the furnace to completely remove surface impurities from the surface before being extruded.
This toothpaste consists of a planetary disk spinning two large balloons. This plate is moved by a three-phase displacement motor with trapezoidal transmission.
On this plate, and set at 120º with each other, there are 3 brushes with steel barbs whose diametrical position can be adjusted independently with a lace mechanism. Once the brush is placed in the correct diameter it can be blocked in this position. In addition, each one of these mechanisms has a spring compensating for the effect of centrifugal force.
In addition, each type of brusher has anti-rotation system to ensure optimal contact between steel bars and aluminum bars.
Machine protection is provided by four screws between them for easy machine maintenance.
The main body has two side windows to connect the suction hose to the suction and filter.
The dust filter system is explosion-proof.
Self-cleaning cartridges by means of automatic washing in reverse flow with compressed air.
The dust accumulated in the cartridge is discharged by means of a hopper in a tight sealed container.
Fireplace Z1 FT / Logs
Heated fireplace heater records the set temperature to optimize energy consumption.
The internal structure is made of heat-resistant ceramic and ceramic fiber, and is specially designed to maintain the temperature and insulation inside the furnace from outside.
The aluminum logs into the furnace at ambient temperature and leaves it at a temperature of around 500ºC. Higher temperatures in the furnace are obtained by independent control of each burning zone.
Between the combustion chamber and the heating chamber in front of a refractory steel bridge with an insulation panel to prevent thermal leaks.
Located in each of the different areas of the furnace, the thermocouples monitor the temperature of the log and record it by direct contact and located on the side to allow easy access for maintenance.
Large gaseous systems benefit from a suction-heat-up turbine that forms combustion areas and through a distributed system of gases on the surface of the billet to high speed. This increases the heat transfer coefficient and produces significant temperature increases.
The logs are guided through the stainless steel floor roller.
For quick and easy maintenance, the head can be easily removed by means of a special lightweight design.

Z1 CC / Hot Shear
Cutting hot cuts before machining at predefined lengths is defined in the functionality of the production program.
Optimizes soft motion during clamping to avoid damaging the workpiece surface.
The special design and strict tolerance of the clamping system allows for very clean cuts with minimal distortion on the embossed head diameter and flat vertical surfaces at both ends to avoid any air trapping when the workpiece is pre-compressed.
High quality hydraulic guide and hydraulic systems provide precise cutting operation.
The rest of the Billet program allows for the work of two billets as if it were fed continuously and reduced to zero.
Z1 RO Loader / Wheelchairs
The feeder transfers the cuttings from the grinding / sawing system to the press.
The translucent movements are made with electrically driven gears and polyurethane teeth belts with integrated steel wire.
High positioning accuracy is controlled by the encoder.
Control of inverter speed.
Accurate and precise operations minimize the dead cycle time and give the exact position of the embryo on the extruded shaft required by the prior press.
The embryo is transported on two mobile arms, operated hydraulically.
The movements of glass shelves are made with hydraulic cylinders and allow for work with two pieces of workpiece.
The control encoder opens, adjusting it to the actual workpiece length (opening the container depending on the actual workpiece length).
Low maintenance requirements.
The solid structure is made of steel and is tied to the floor to avoid vibration on the system.

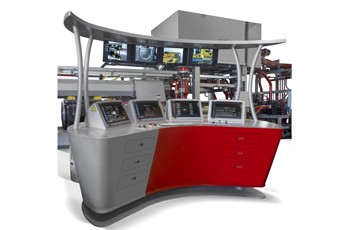

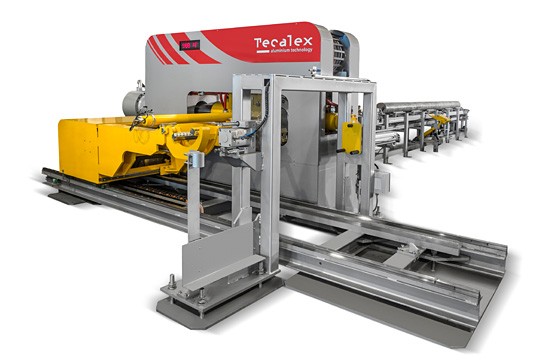
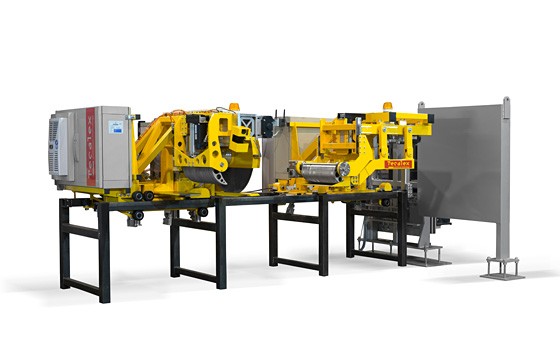